Challenge: Replacing Urethane Cast Parts for Improved Scalability
BIOLASE, a leading medical device company specializing in laser systems and dental imaging equipment, needed a more efficient way to manufacture a critical component for an upcoming medical device launch.
Previously, the part was produced using urethane casting, which posed several limitations:
- Low production efficiency – Each master tool had a limited lifespan of 25-30 parts and a 3-month shelf life.
- Long turnaround times – Urethane casting required 5-8 weeks for each batch.
- Cost constraints – Design iterations were expensive, slowing down development.
BIOLASE needed a faster, scalable, and cost-effective solution to support their goal of producing thousands of parts annually.
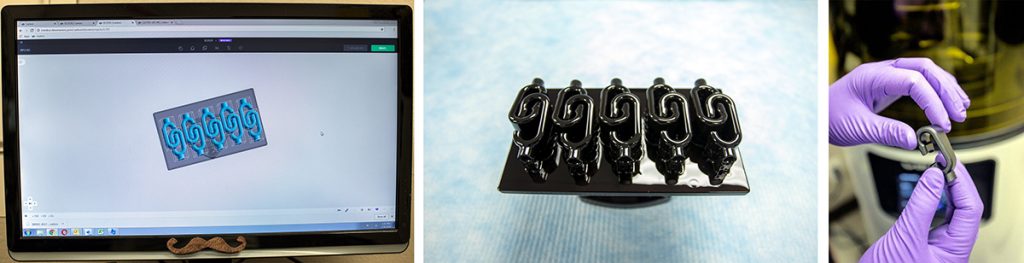
Solution: Carbon’s Digital Light Synthesis™ (DLS) Technology
BIOLASE partnered with Dinsmore Inc., a trusted expert in additive manufacturing, to replace urethane casting with a high-performance 3D printed solution.
Dinsmore’s engineering team selected Carbon’s M Series 3D printers and RPU 60 material, a rigid polyurethane known for its:
- Superior strength and durability compared to urethane.
- Scalability for higher production volumes.
- Faster turnaround times, enabling rapid iteration and validation.
By leveraging Carbon’s Digital Light Synthesis™ (DLS) technology, Dinsmore helped BIOLASE transition to a more agile production process while reducing costs and time to market.
Results: Accelerated Production & Cost Savings
Dinsmore’s Design for Prototyping® and Additive Manufacturing expertise enabled BIOLASE to:
- Reduce development time by 70% – The final design was approved within two weeks, drastically accelerating the go-to-market timeline.
- Lower production costs – BIOLASE expects to save over $10,000 annually in bill of materials (BOM) costs.
- Eliminate tooling constraints – Unlike urethane casting, 3D printing requires no master tools, allowing for seamless part modifications and on-demand production.
“While urethane casting worked in the past, the process didn’t meet our cost and turnaround time requirements. Additive manufacturing with Dinsmore’s expertise gave us a high-quality part, at reasonable cost, that can be produced at scale.” — Julio Cely, Mechanical Engineer, BIOLASE
Conclusion: A Scalable, Future-Ready Manufacturing Process
By transitioning from urethane casting to additive manufacturing, BIOLASE not only gained a higher-performing part but also optimized efficiency, cost, and production speed.
“Our work with BIOLASE and Carbon’s DLS technology showcases our expertise in additive manufacturing and rapid prototyping. We’re excited to continue helping customers across industries bring their products to market faster.” — Jay Dinsmore, CEO & Founder, Dinsmore Inc.
This successful collaboration demonstrates how advanced additive manufacturing can replace traditional processes, enabling greater agility, scalability, and cost savings—essential for the future of medical device production.