Our domestic injection molding capabilities are fueled by the dedicated team at our HARBEC business. With more than 45 years of experience, we offer superior strength and product durability, fast production speeds, and the capacity to meet the need for high production volumes.
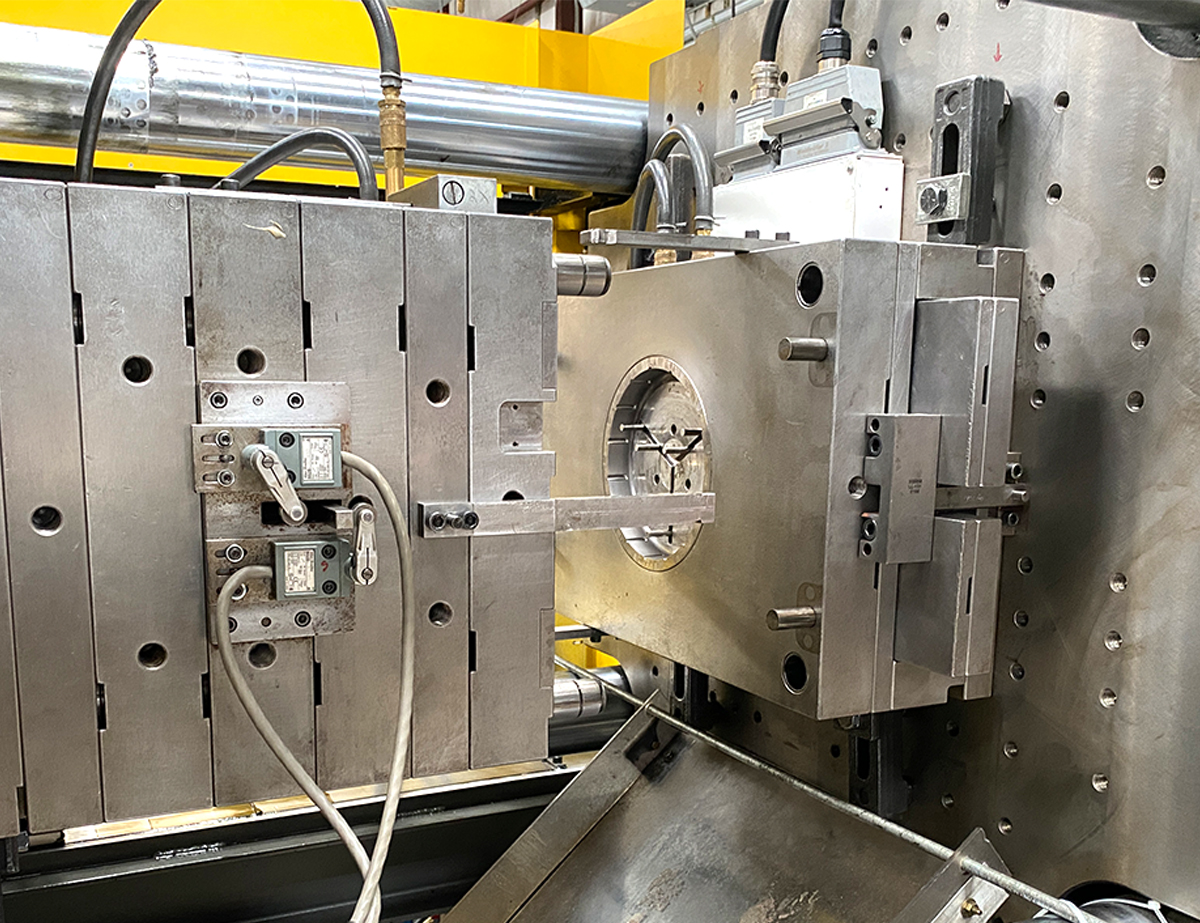
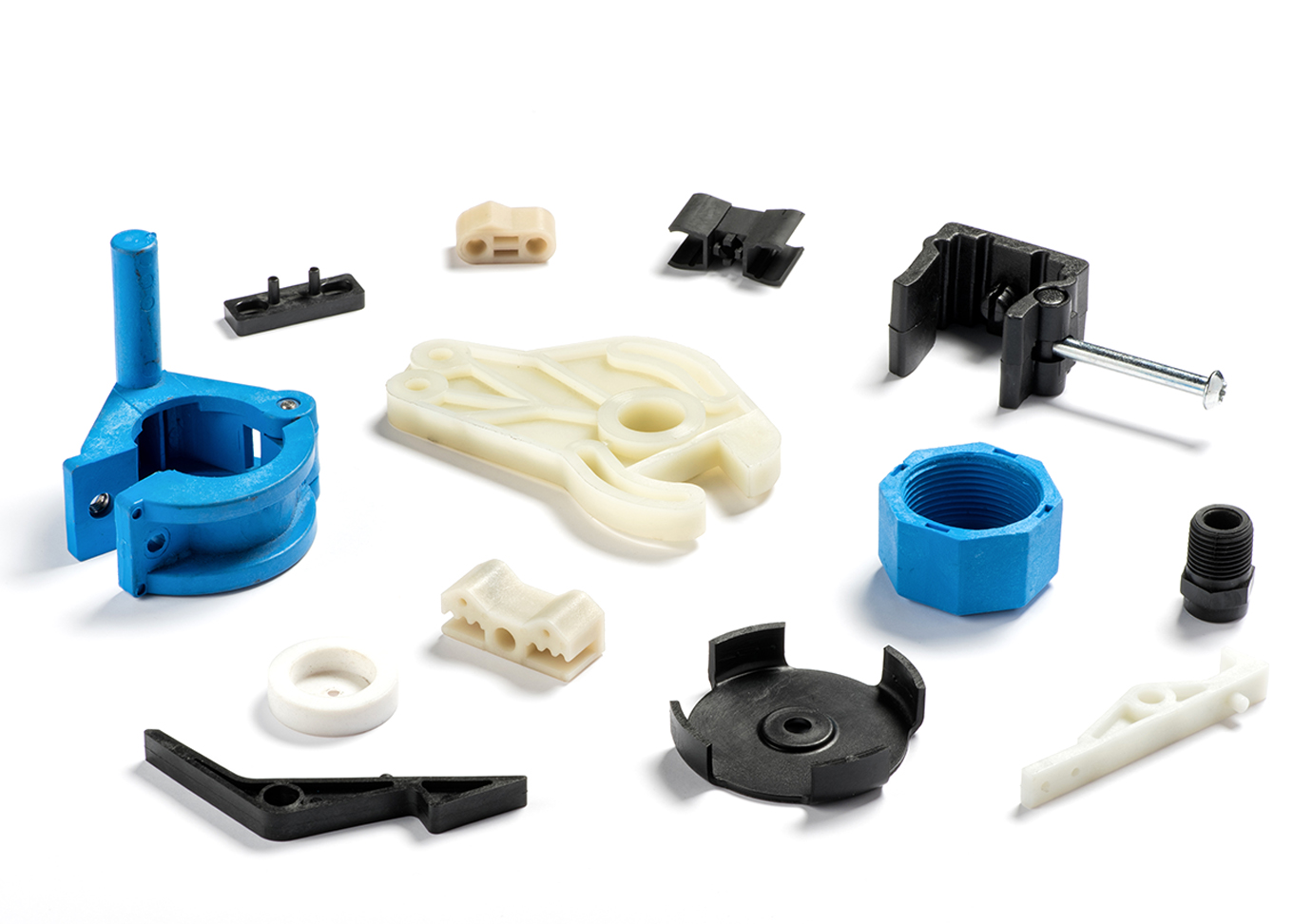
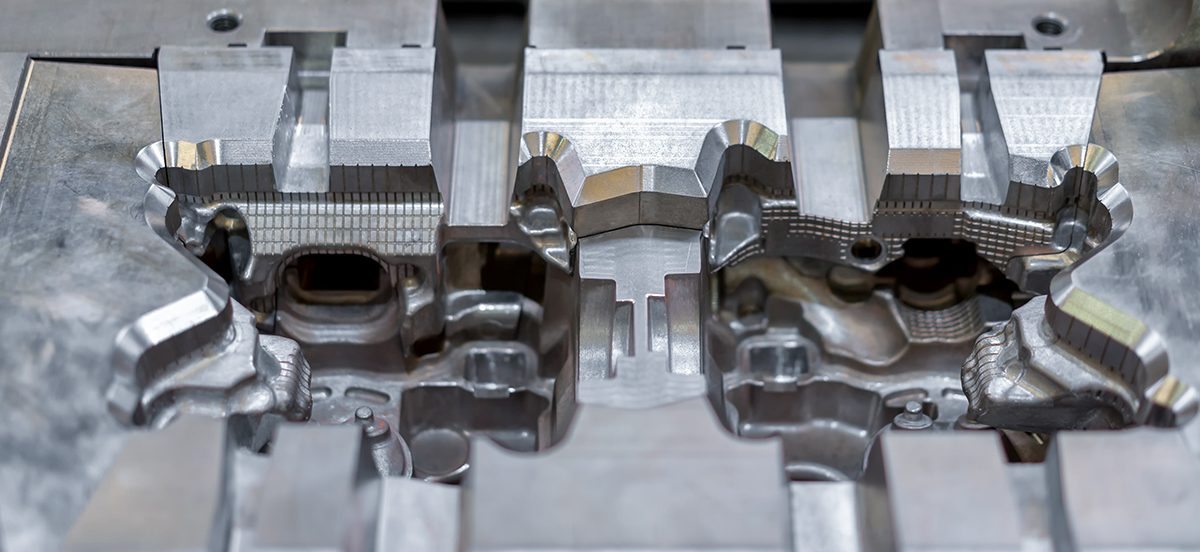
ADDMAN offers a range of in-house secondary operations that are necessary to meet specific appearance specifications, performance requirements, and dimensional tolerances that may not be achievable with plastic parts produced directly from an injection-molding press. These secondary operations include gate trimming, CNC-machining (such as drilling, reaming, and surfacing), annealing, and water treating.
ADDMAN provides top-quality assembly services across a wide range of applications, from simple part joining to the production of complex electro-mechanical devices. Our tool-making expertise allows us to design and build fixtures that minimize costs for our customers.
Additionally, we frequently produce all the necessary components for assemblies that require plastic and metal parts. Our skilled team of experts utilizes various assembly processes such as manual assembly, ultra-sonic and heat welding, heat staking, bonding, taping, and labeling to deliver high-quality finished products that meet our clients’ exacting standards.
ADDMAN’s decorating capabilities offer our clients the ability to achieve the desired cosmetic appearance or surface performance of their parts beyond what is achievable with natural plastic or metal finishes. Whether it’s the visual demands of consumer sporting goods or the electro-chemical requirements of industrial products, we have established subcontractor relationships for painting, plating, hot stamping, and pad printing. With our expertise and attention to detail, we ensure that the end result meets our clients’ exacting specifications.
ADDMAN provides comprehensive logistics services to complement our part and assembly manufacturing capabilities, including reusable packaging, kitting, inventory management, and distribution and fulfillment.
Our logistics services cover all aspects of the supply chain, from package design and shipment-return loop management to component manufacture and ordering, production planning, and order fulfillment.
By leveraging our expertise in logistics management, we ensure that our clients receive their parts and assemblies on time and in optimal condition.
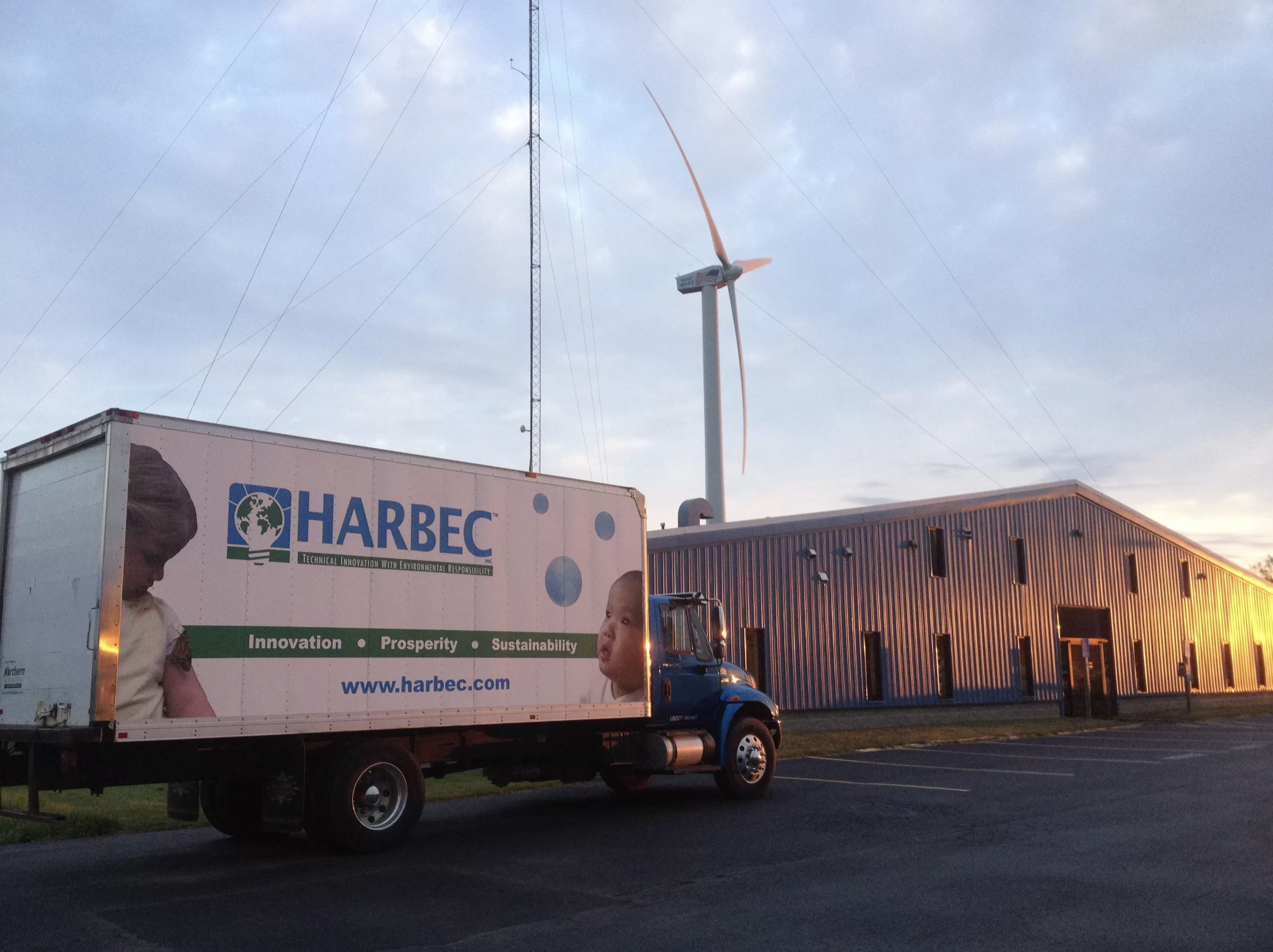