Functional prototyping is the crucial bridge between initial design concepts and full-scale production. At Dinsmore, a part of the ADDMAN Group, we specialize in creating high-quality functional prototypes that validate your design, functionality, and manufacturability, ensuring a smooth transition to mass production.
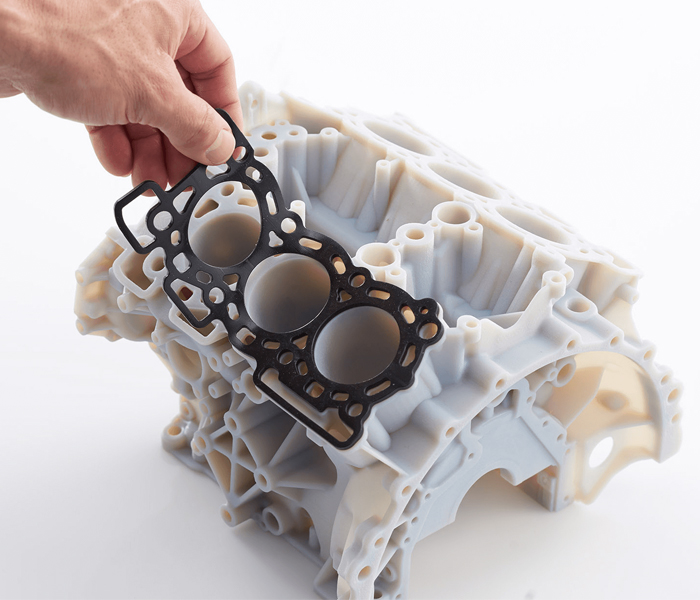
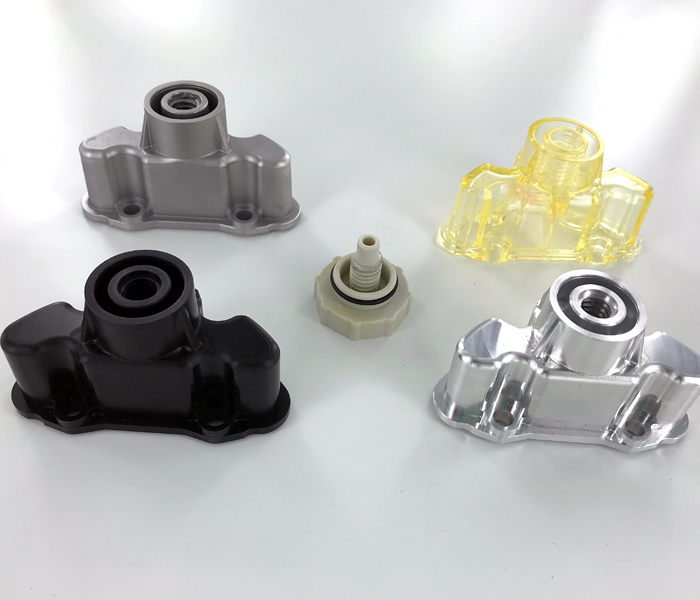
Our Manufacturing Techniques
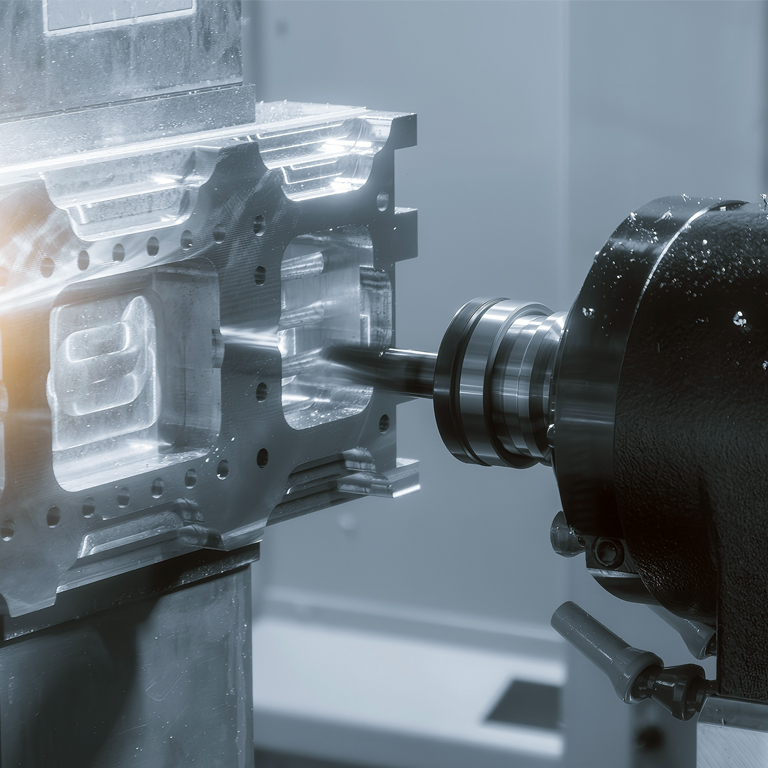
CNC Machining
Offers high precision and is suitable for tight tolerances and complex geometries across a wide range of materials.
- Material Versatility: CNC machining can handle a wide range of materials, including metals (such as aluminum, steel, and titanium), plastics (like ABS, PLA, and nylon), and composites (such as carbon fiber and glass fiber). This versatility allows us to choose the best material for your prototype’s specific requirements.
- Precision and Accuracy: CNC machines operate with high precision, ensuring that each part is manufactured to exact specifications. This is particularly important for prototypes that must meet stringent design tolerances.
- Complex Geometries: The advanced capabilities of CNC machining allow for the creation of complex geometries that would be difficult or impossible to achieve with other manufacturing methods. This includes intricate internal features and detailed surface finishes.
- Consistency and Repeatability: CNC machining provides consistent results, making it possible to produce multiple identical prototypes with the same high level of accuracy. This is essential for validating design and functionality before moving to batch production.
- Fast Turnaround: With CNC machining, we can quickly produce high-quality prototypes, reducing lead times and allowing for faster design iteration and validation.
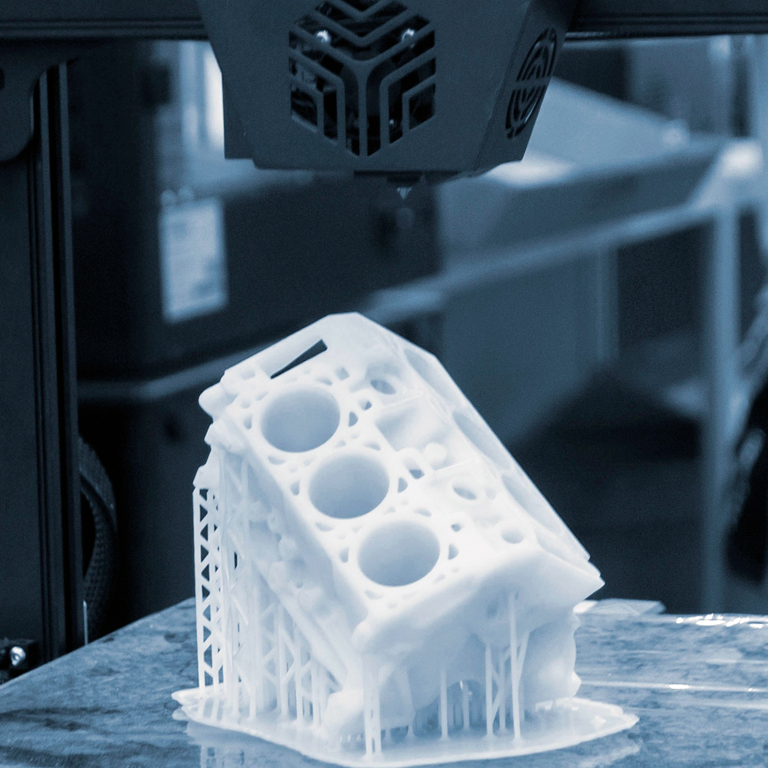
Additive Manufacturing
This technology offers unparalleled flexibility and speed, making it an ideal choice for producing intricate and complex designs.
- Fused Deposition Modeling (FDM): This method is well-suited for creating durable prototypes with complex geometries. It’s particularly beneficial for producing functional parts that require strength and stability.
- Stereolithography (SLA): This technology is ideal for producing parts with fine features and smooth surface finishes, making it perfect for applications where precision is critical.
- Material Options: Supports a wide variety of materials. This allows for the creation of prototypes that closely mimic the final product in terms of both appearance and functionality.
- Speed and Efficiency: Prototypes can be created quickly, allowing for faster iteration and refinement of designs. This is especially useful in the early stages of product development when multiple versions of a prototype may be needed.
- Cost-Effective: It reduces material waste and allows for the production of complex parts without the need for expensive tooling.
- Complex Geometries: Enables the creation of highly complex geometries including internal structures, overhangs, and intricate details.
- Customization: This flexibility is particularly advantageous for creating prototypes that need to fit unique design criteria or specialized functions.
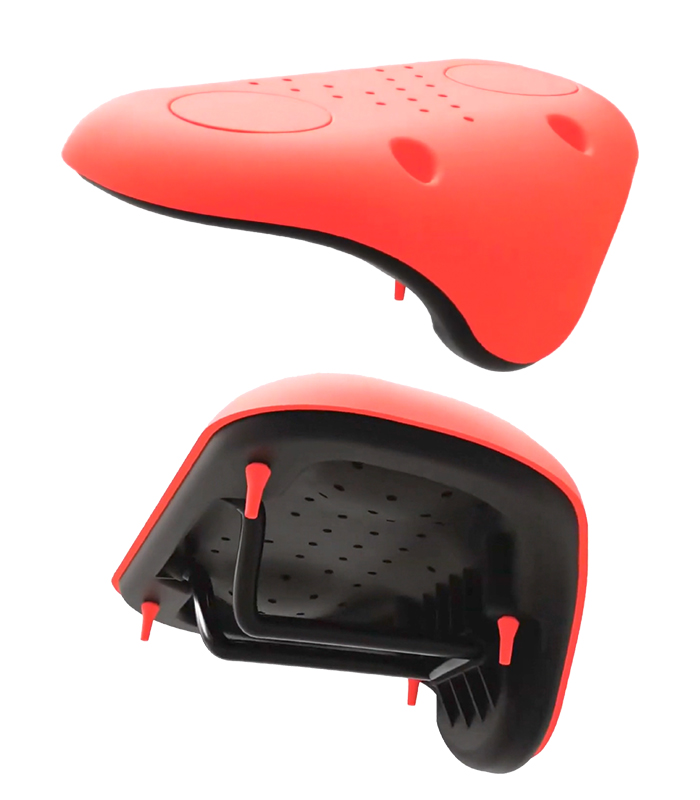