Titanium alloys combine high strength, low weight, and exceptional corrosion resistance, making them the material of choice for aerospace, medical, defense, and high-performance industrial applications.
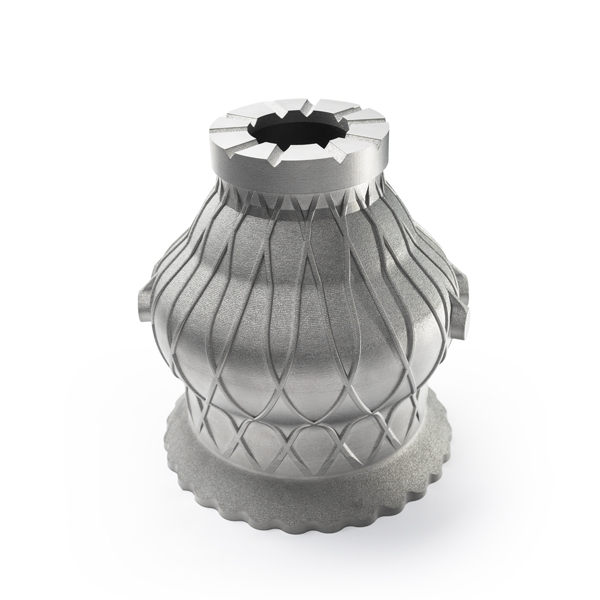
Below is an overview of the titanium alloys available and their unique advantages:
The most commonly used titanium alloy, offering high strength, toughness, and corrosion resistance.
- Ideal Applications: Aircraft frames, medical implants, automotive racing components, and defense armor.
- Unique Characteristics: Excellent fatigue resistance and biocompatibility, making it ideal for aerospace and medical applications.
A highly formable titanium alloy with moderate strength and corrosion resistance.
- Ideal Applications: Hydraulic tubing, marine components, and sports equipment.
- Unique Characteristics: Lightweight yet strong, with excellent weldability and seawater resistance.
A high-performance alloy with enhanced high-temperature strength, commonly used in aerospace propulsion.
- Ideal Applications: Jet engine components, turbine blades, and structural aerospace parts.
- Unique Characteristics: High oxidation resistance and thermal stability at elevated temperatures.
A versatile class of titanium alloys offering high strength, toughness, and excellent cold formability.
- Ideal Applications: Fasteners, landing gear, and high-performance sporting goods.
- Unique Characteristics: Improved ductility and ease of processing compared to traditional titanium alloys.
Commercially pure titanium with increasing levels of strength and hardness.
- Ideal Applications: Chemical processing, medical implants, and desalination plants.
- Unique Characteristics: Superior biocompatibility and corrosion resistance, particularly in harsh environments.
Titanium alloys offer the strength of steel at nearly half the weight, making them an optimal material for industries where reducing mass enhances efficiency, fuel economy, and overall performance. This high strength-to-weight ratio allows for lightweight yet durable components in applications where structural integrity cannot be compromised.
- Why It Matters: Lower weight improves fuel efficiency, speed, and payload capacity in aerospace and automotive applications, while maintaining the structural strength needed for high-stress environments.
- Applications:
- Aircraft fuselage and landing gear reduce fuel consumption and increase payload capacity.
- High-performance automotive parts improve acceleration and handling while maintaining durability.
- Lightweight armor for military vehicles and protective gear enhances mobility without sacrificing protection.
Titanium alloys naturally resist oxidation, rust, and chemical degradation, even in severe environmental conditions. Their corrosion resistance makes them highly valuable in marine, aerospace, medical, and chemical processing industries where exposure to moisture, saltwater, or aggressive chemicals can rapidly degrade other metals.
- Why It Matters: Corrosion-resistant materials last longer, reduce maintenance costs, and improve safety in demanding applications. Titanium’s ability to resist seawater, acids, and industrial chemicals allows it to outperform traditional stainless steel and aluminum in extreme environments.
- Applications:
- Seawater-exposed components in submarines, ship propellers, and offshore oil rigs.
- Corrosion-resistant piping and heat exchangers in chemical plants.
- Surgical tools and implants that resist body fluids and sterilization processes without degradation.
Titanium alloys can endure repetitive stress, vibrations, and cyclic loading without failing due to fatigue or cracking. This makes them indispensable in applications where materials undergo continuous mechanical strain, such as aircraft, medical implants, and industrial machinery.
- Why It Matters: Fatigue resistance is critical for long-term reliability, reducing the risk of structural failure in mission-critical systems. Components must maintain their integrity under constant mechanical stress and exposure to extreme environmental conditions.
- Applications:
- Aircraft wings and structural components experience high vibration and repetitive stress during flight.
- Orthopedic implants such as hip and knee replacements must endure years of movement and pressure inside the body.
- Industrial turbines and rotating machinery must operate under continuous stress cycles without cracking.
Titanium alloys withstand extreme heat and high thermal stress while maintaining their mechanical properties. With a melting point exceeding 1,600°C (3,000°F), titanium remains strong in high-temperature aerospace, automotive, and industrial applications where lesser materials would weaken, deform, or oxidize.
- Why It Matters: Many industries operate in environments where materials are exposed to prolonged high temperatures, requiring metals that won’t weaken under intense thermal loads. Titanium alloys provide the stability and strength necessary to operate under extreme heat conditions.
- Applications:
- Jet engine and turbine blades require extreme heat resistance to withstand the high temperatures of combustion.
- Rocket propulsion systems rely on titanium components that endure the extreme conditions of re-entry.
- Automotive exhaust systems and racing components use titanium for its ability to handle high-performance heat loads.
Titanium is one of the most biocompatible metals, meaning it is non-toxic, non-allergenic, and well-tolerated by the human body. This makes it the material of choice for medical implants, prosthetics, and surgical instruments, where safety and longevity are paramount.
- Why It Matters: Unlike other metals, titanium does not react with body fluids, corrode inside the body, or cause immune system rejection. It also promotes osseointegration, allowing bone tissue to bond directly with titanium implants, ensuring superior implant stability.
- Applications:
- Orthopedic implants, including artificial joints, bone plates, and screws for fracture repair.
- Dental implants used for permanent tooth replacement.
- MRI-compatible surgical tools that require non-magnetic properties for imaging procedures.
Titanium alloys are widely used in aerospace and defense due to their high strength-to-weight ratio, heat resistance, and corrosion resistance. These properties make them ideal for aircraft structures, military vehicles, and propulsion systems that must endure extreme conditions without adding unnecessary weight.
- Aircraft Fuselages, Wings, and Landing Gear
Titanium reduces overall aircraft weight while maintaining durability and crash resistance. It is used in commercial and military aircraft to improve fuel efficiency and increase payload capacity. - Jet Engine Components and Turbine Blades
Jet engines operate under extreme heat and mechanical stress. Titanium alloys are used in fan blades, compressor discs, and turbine casings for their high-temperature stability and oxidation resistance. - Lightweight Armor and Structural Military Components
Titanium’s high-impact resistance and ability to absorb ballistic energy make it valuable for military applications. It is used in armored vehicles, body armor plates, and military-grade aircraft, enhancing protection while maintaining mobility.
Titanium alloys provide corrosion resistance in saltwater environments, making them ideal for shipbuilding, offshore structures, and marine propulsion systems.
- Corrosion-Resistant Hulls, Propellers, and Heat Exchangers
Ships and submarines require materials that can resist long-term saltwater exposure. Titanium is used in ship hulls, propellers, and cooling systems to enhance longevity and reduce maintenance. - Seawater Piping and Desalination Plant Components
Titanium piping is widely used in desalination plants and offshore rigs, where exposure to seawater and industrial chemicals is unavoidable. It provides long service life with minimal maintenance. - Submarine Components Requiring Extreme Durability
Titanium is used in deep-sea applications where pressure resistance is critical. It is found in submersible frames, pressure-resistant bulkheads, and high-pressure piping systems.
Titanium is widely used in industrial manufacturing and chemical processing, where exposure to high heat, pressure, and corrosive chemicals requires superior material performance.
- Heat Exchangers and Pressure Vessels
Titanium heat exchangers and pressure vessels withstand extreme temperatures and aggressive chemical environments, ensuring long operational life in refineries and power plants. - Titanium Piping for High-Temperature, Corrosive Applications
Industrial piping must handle extreme heat and pressure fluctuations. Titanium is commonly used in chemical transport systems, geothermal energy production, and industrial cooling lines. - Tooling and Fixtures in High-Performance Manufacturing
Titanium’s hardness and wear resistance allow for extended use in precision machining and metal forming applications. It is found in aerospace tooling, injection molding, and high-speed machining applications.
Titanium is used in high-performance automotive applications where strength, weight reduction, and heat resistance are essential.
- High-Performance Exhaust Systems, Valves, and Connecting Rods
Titanium exhaust systems improve fuel efficiency and reduce weight while maintaining heat resistance. It is also used in engine valves and connecting rods for durability under high RPM conditions. - Racing Chassis and Suspension Components
Motorsports rely on titanium for its combination of strength and flexibility. It is used in chassis, suspension systems, and critical fasteners to improve performance and durability. - Lightweight Structural Parts for Improved Speed and Efficiency
Titanium is used in crash-resistant frames, electric vehicle battery enclosures, and aerospace-grade body components to enhance aerodynamics and reduce overall vehicle weight.
Titanium is widely used in medical applications due to its biocompatibility, durability, and corrosion resistance. Its non-reactive nature makes it ideal for surgical guides, precision instruments, and medical devices that require strength, sterilization compatibility, and long-term reliability in clinical environments.
- Titanium Orthopedic Implants, Including Hip and Knee Replacements
Titanium is a preferred material for load-bearing implants because it bonds with bone and resists wear. Hip and knee replacements made from titanium provide long-term durability and reliability. - Dental Implants and Surgical Instruments
Titanium dental implants provide a permanent solution for tooth replacement, integrating seamlessly with the jawbone. Surgical instruments made from titanium remain sterile, lightweight, and corrosion-resistant. - MRI-Compatible Medical Devices
Unlike stainless steel, titanium is non-magnetic, making it safe for MRI scans and other imaging technologies. This property is essential for implants, prosthetics, and surgical tools used in hospitals and diagnostic centers.
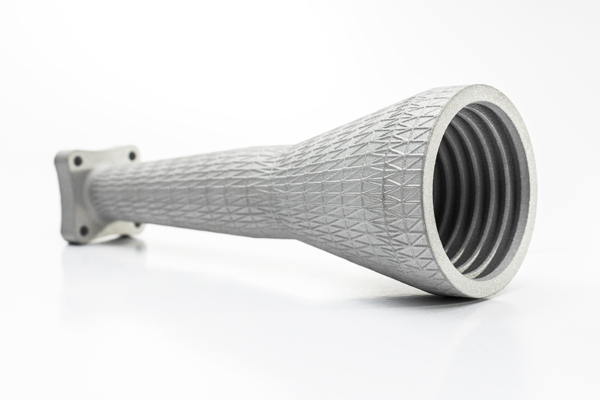