Explore ADDMAN’s versatile range of thermoplastics, including polycarbonate, PEKK, and medical-grade options, designed for demanding industries like aerospace, automotive, and medical devices.
Below is an overview of the polyurethane-based polymers available and their unique advantages:
A tough, transparent thermoplastic with excellent impact resistance and high heat tolerance.
- Ideal Applications: Lenses, electrical components, and enclosures for industrial and consumer products.
- Unique Characteristics: Combines clarity with high durability and thermal stability.
A strong and impact-resistant blend of polycarbonate and ABS.
- Ideal Applications: Automotive panels, electronic housings, and lightweight brackets.
- Unique Characteristics: Offers superior toughness, thermal resistance, and ease of processing.
A biocompatible, sterilizable thermoplastic ideal for medical and healthcare applications.
- Ideal Applications: Surgical guides, diagnostic tools, and sterilizable equipment housings.
- Unique Characteristics: Certified for bioco
A high-performance thermoplastic with exceptional chemical resistance and heat tolerance.
- Ideal Applications: Aerospace ducts, medical devices, and industrial fluid-handling components.
- Unique Characteristics: Withstands extreme temperatures and aggressive chemicals without degrading.
A high-strength, heat-resistant thermoplastic with excellent chemical resistance.
- Ideal Applications: Aerospace and defense components, custom tooling, and parts exposed to extreme environments.
- Unique Characteristics: Exceptional strength-to-weight ratio and dimensional stability under heat and stress.
A specialty thermoplastic designed for applications requiring precision and durability.
- Ideal Applications: Automotive components, industrial parts, and lightweight enclosures.
- Unique Characteristics: High impact resistance and excellent surface finish capabilities.
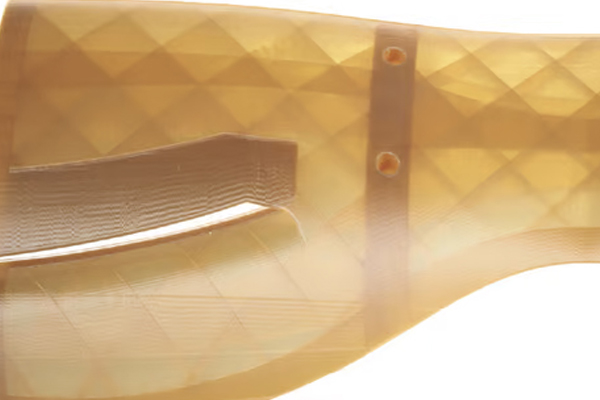
Thermoplastics such as PPSF/PPSU and Antero 800 (PEKK) are designed to perform reliably in extreme heat environments. These materials retain their mechanical properties and dimensional stability at high operating temperatures, making them ideal for heat-intensive industries like aerospace and energy.
- Why It Matters: Thermal resistance allows components to function effectively in environments where standard plastics would degrade or fail, ensuring consistent performance.
- Applications:
- Jet engine components and aerospace ducting exposed to high temperatures.
- Automotive parts like under-hood housings and heat shields.
- Industrial tooling and fixtures used in high-temperature manufacturing processes.
Thermoplastics are highly resistant to exposure from oils, solvents, fuels, and aggressive chemicals, ensuring durability in environments where chemical degradation is a concern. Materials such as PPSF/PPSU and PC-ABS are particularly suited for applications where contact with corrosive agents is unavoidable.
- Why It Matters: Chemical resistance reduces wear and tear, extends part lifespan, and minimizes maintenance needs, even in chemically harsh environments.
- Applications:
- Industrial fluid-handling components like valves and seals.
- Medical device housings exposed to sterilizing agents and cleaning chemicals.
- Automotive fuel system components and engine bay parts exposed to oils and fuels.
Medical-grade thermoplastics like PC-ISO are specifically designed to endure autoclaving, gamma radiation, and chemical sterilization processes. These materials maintain their mechanical properties and dimensional accuracy even after repeated sterilization cycles, ensuring reliability in healthcare and medical applications.
- Why It Matters: Compatibility with sterilization processes is critical for medical devices that must meet stringent hygiene and safety standards. Durable materials reduce replacement frequency and enhance patient safety.
- Applications:
- Surgical guides and diagnostic tools requiring sterilization after every use.
- Housings for portable medical equipment that must withstand cleaning agents.
- Components for implantable or diagnostic devices requiring biocompatibility.
Thermoplastics are highly adaptable, compatible with various manufacturing methods such as additive manufacturing (3D printing), injection molding, and CNC machining. This versatility allows manufacturers to create complex geometries, detailed prototypes, and precision-engineered end-use parts with exceptional efficiency.
- Why It Matters: The ability to use thermoplastics across different manufacturing processes offers flexibility in design and production, enabling rapid prototyping and scalable production for a variety of industries.
- Applications:
- Intricate 3D-printed components with complex geometries and high detail.
- High-volume injection-molded parts for automotive and consumer products.
- CNC-machined fixtures and tooling for industrial production lines.
High-performance thermoplastics play a crucial role in aerospace and defense applications, where lightweight durability, chemical resistance, and thermal stability are essential. These materials enable advanced designs that improve efficiency while maintaining safety and reliability.
- Lightweight Brackets, Structural Components, and Custom Tooling with Antero 800
Antero 800 (PEKK) provides exceptional strength-to-weight ratios, making it ideal for reducing aircraft weight while maintaining structural integrity.- Applications: UAV brackets, aircraft structural supports, and custom 3D-printed tools for maintenance.
- Heat- and Chemical-Resistant Ducts and Enclosures Made from PPSF/PPSU
PPSF/PPSU materials excel in environments where components are exposed to extreme heat and aggressive chemicals, ensuring durability and functionality over time.- Applications: High-temperature exhaust ducts, fuel line enclosures, and protective casings for aerospace systems.
Thermoplastics offer automotive manufacturers lightweight, durable solutions that enhance vehicle performance and improve fuel efficiency while maintaining safety standards.
- Impact-Resistant Panels and Lightweight Structural Parts with PC-ABS
PC-ABS blends combine the durability of polycarbonate with the ease of processing of ABS, making them ideal for components that require both strength and flexibility.- Applications: Interior panels, under-hood parts, and crash-resistant mounts.
- High-Strength Brackets and Durable Housings Using BASF 3280
BASF 3280 is engineered for high-impact resistance and surface finish quality, making it suitable for structural and aesthetic applications in modern vehicles.- Applications: Engine bay housings, mirror brackets, and exterior trim components.
In the medical field, thermoplastics are trusted for their biocompatibility, sterilization compatibility, and chemical resistance, enabling the production of safe and reliable medical equipment.
- Sterilizable Housings, Surgical Guides, and Diagnostic Tools Made from PC-ISO
PC-ISO is a medical-grade polycarbonate that withstands repeated sterilization without losing its mechanical integrity, ensuring safety in healthcare settings.- Applications: Housings for diagnostic devices, custom surgical guides, and biocompatible casings for portable medical equipment.
- Chemical-Resistant Components for Medical Equipment with PPSU
PPSU materials resist aggressive cleaning agents and sterilization processes, making them ideal for medical devices exposed to harsh environments.- Applications: Surgical instrument components, sterilizable fluid-handling systems, and long-term-use diagnostic tools.
Thermoplastics deliver exceptional performance in industrial applications where components must endure extreme environments, heavy loads, and constant use.
- Custom Tooling and Jigs Made with PEKK for Extreme Environments
PEKK’s high thermal and chemical resistance make it ideal for industrial tooling and fixtures exposed to harsh manufacturing conditions.- Applications: High-temperature molds, chemical-resistant assembly jigs, and tooling for precision manufacturing.
- High-Performance Machine Enclosures and Fixtures with PPSU and PC-ABS
PPSU and PC-ABS provide strength and durability for industrial equipment enclosures and fixtures, ensuring long-term reliability and protection.- Applications: Protective casings for high-stress machinery and fixtures for automated assembly lines.
Thermoplastics enable the production of durable, lightweight, and visually appealing consumer products. Their versatility allows manufacturers to create components that meet both functional and aesthetic requirements.
- Durable, High-Quality Enclosures for Electronics and Appliances with PC
Polycarbonate’s impact resistance and smooth finish make it an ideal material for creating reliable and attractive consumer electronics and appliance housings.- Applications: Laptop casings, remote control housings, and protective covers for small appliances.
- Wear-Resistant Components and Ergonomic Designs with PC-ABS
PC-ABS blends are valued for their ability to produce strong, comfortable, and wear-resistant components for everyday use.- Applications: Tool handles, sports equipment, and impact-resistant mobile device cases.