We lead the industry with Stereolithography (SLA) and Fine Resolution Stereolithography (FRSLA®), offering a carefully selected range of resins designed for exceptionally high resolutions. Our trademark technology ensures unmatched precision and accuracy in additive manufacturing, delivering exceptional results for a wide variety of applications.
Polymer Additive
SLA/FRSLA

Precision and Clarity
Stereolithography (SLA) uses a UV laser to cure and solidify liquid photopolymer resin, layer by layer, into a precise 3D object. It is one of the most established and widely used additive manufacturing processes, known for its ability to produce high-resolution parts with smooth surface finishes and fine details. FRSLA® is specifically engineered for small-sized parts or components that demand intricate detail and the highest resolution, while SLA accommodates a broader range of applications across industries.
Key Benefits:
- Exceptional Resolution: Both SLA and FRSLA are optimized to produce parts with fine detail and precise accuracy, making them ideal for parts that require intricate geometries or superior surface finishes.
- Smooth Surface Finish: The seamless layer bonding ensures smooth, high-quality surfaces, suitable for creating Class A models and visually appealing prototypes.
- Dimensional Accuracy: Achieve exact tolerances and precise fits for your parts, critical for applications in automotive, aerospace, and biomedical industries.
- Air and Watertightness: Our SLA and FRSLA prints provide superior air and watertight properties, essential for components in demanding environments.
- Large Build Platforms: Handle large parts and complex assemblies with our expansive build capabilities, making SLA a versatile solution for both small and large-scale projects.
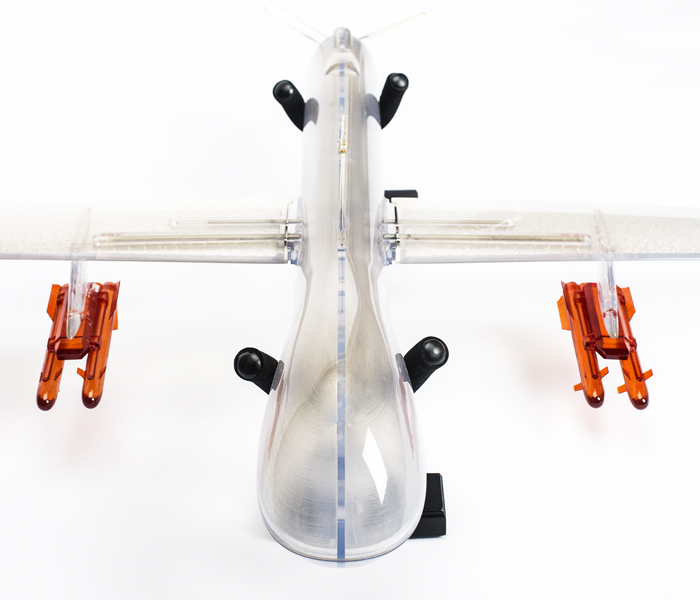
Applications
Known for its ability to create smooth, accurate, and complex designs, SLA is widely used across industries for a variety of applications, from prototyping to final-use parts.
- Scale Models: Create highly detailed, scale-accurate models for architecture, engineering, or product design.
- Optical Lenses: Manufacture transparent, finely detailed optical components with smooth surfaces.
- Medical Modeling: Produce precise anatomical models for surgical planning, medical education, or device testing.
- Casting Patterns: Build accurate patterns for casting processes, offering high resolution and clean surface finishes.
- Large Parts: Handle large-scale components with excellent dimensional stability, enabling the production of sizable assemblies.