Refractory metals are the champions of high-temperature, high-stress environments. From hypersonic propulsion systems to nuclear reactors, their unparalleled heat resistance and strength power innovation in the most demanding industries.
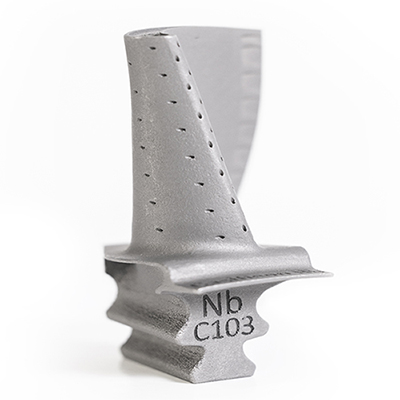
Below is an overview of the refractory alloys available and their unique advantages:
Lightweight, corrosion-resistant, and designed for extreme heat applications.
- Ideal Applications: Hypersonic propulsion systems, rocket nozzles, and satellite components.
- Unique Characteristics: Combines lightweight properties with exceptional oxidation resistance.
Known for its unmatched density, high melting point (3,422°C), and exceptional hardness.
- Ideal Applications: Rocket nozzles, industrial tooling, and X-ray shielding.
- Unique Characteristics: High thermal conductivity, resistance to radiation damage, and extreme weight for use in ballast and counterweights.
Lightweight and strong with excellent thermal and electrical conductivity.
- Ideal Applications: Nuclear reactor components, furnace parts, and electronics.
- Unique Characteristics: High creep resistance and compatibility with high-temperature coatings.
Highly corrosion-resistant with excellent biocompatibility.
- Ideal Applications: Chemical processing equipment, medical implants, and electronics.
- Unique Characteristics: Can endure harsh acid environments and resist thermal fatigue.
Rare and incredibly heat-resistant, often alloyed with tungsten or molybdenum.
- Ideal Applications: Jet engines, rocket thrusters, and high-performance heat exchangers.
- Unique Characteristics: Outstanding thermal shock resistance and unmatched high-temperature stability.
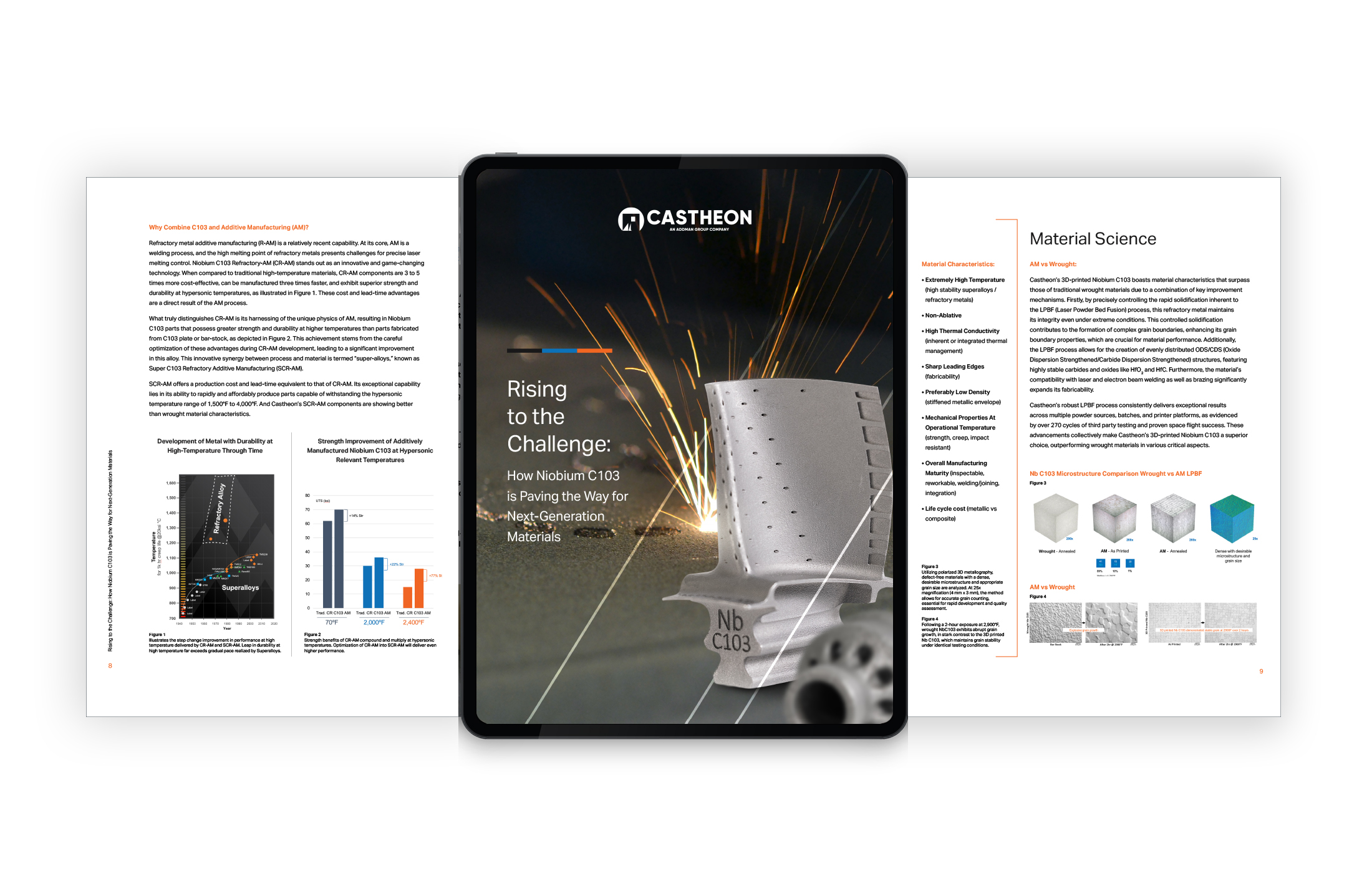
Refractory metals are defined by their extraordinary ability to withstand extreme heat without melting or softening. With melting points often exceeding 2,000°C (3,632°F), these materials are ideal for environments such as rocket propulsion systems, high-temperature furnaces, and industrial tooling. They outperform conventional materials that would fail under similar conditions.
Examples: Tungsten’s melting point of 3,422°C and tantalum’s 3,017°C are among the highest of all metals.
Unlike many materials that weaken or deform at high temperatures, refractory metals maintain their mechanical strength and integrity under thermal stress. This makes them indispensable for critical applications such as aerospace engine components, where materials must perform reliably under extreme heat and pressure.
Why It Matters: Maintaining strength under heat prevents failures in applications like hypersonic vehicles and nuclear reactors.
Refractory metals resist oxidation and chemical degradation, even in highly corrosive or reactive environments. This characteristic makes them highly sought after in chemical processing, power generation, and aerospace propulsion, where exposure to harsh chemicals and extreme conditions is common.
Examples: Tantalum resists nearly all acids, while niobium alloys excel in oxidizing environments.
Refractory metals efficiently transfer heat and electricity, making them critical for applications requiring thermal management or electrical conductivity. Their ability to dissipate heat effectively enhances performance and safety in systems like electronics, heat exchangers, and rocket nozzles.
Applications: Tungsten’s thermal conductivity is essential for heat shields, while molybdenum’s electrical conductivity supports advanced electronic components.
Refractory metals maintain their shape and structural integrity under high mechanical loads, even at elevated temperatures. This resistance to creep and deformation ensures long-term reliability in high-stress environments, such as turbine blades, furnace components, and defense systems.
Examples: Molybdenum and rhenium alloys are specifically designed to resist creep in high-temperature applications.
- Wear Resistance: Refractory metals are highly resistant to abrasion, making them ideal for tooling and molds used in high-stress manufacturing processes.
- Density and Weight Versatility: High-density materials like tungsten are used for radiation shielding, while lightweight niobium alloys are perfect for aerospace applications.
- Customizability: Refractory metals can be alloyed with other materials to enhance specific properties, such as ductility, oxidation resistance, or machinability.
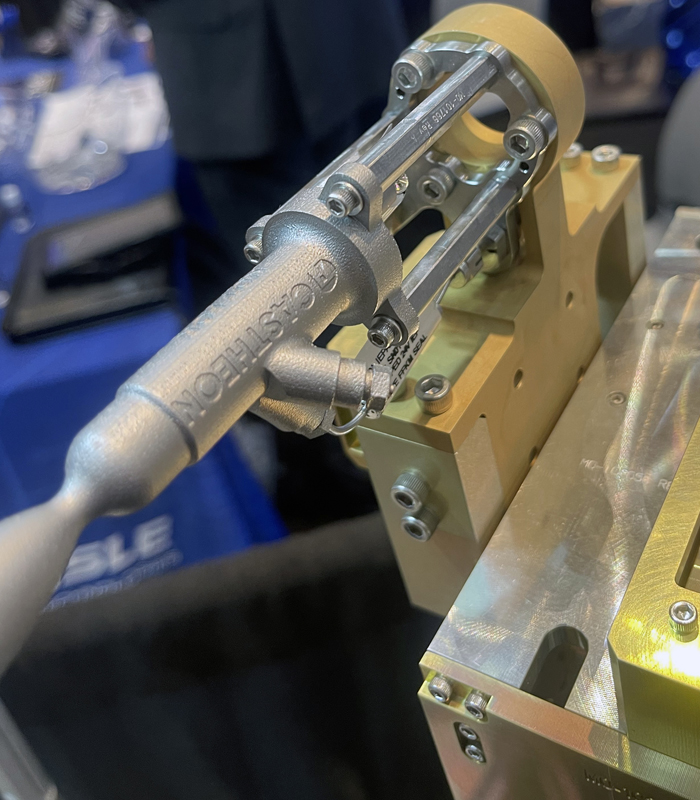
- Rocket nozzles and thrusters.
- Hypersonic vehicle components.
- Combustion chambers and heat shields.
- Munitions and armor plating.
- High-performance components for hypersonic weapons.
- Nuclear reactor components and heat exchangers.
- Chemical processing equipment and reactor linings.
- Furnace components and molds for high-temperature manufacturing.
- Tooling for die-casting and extrusion processes.
