Polyphenylsulfone (PPSF/PPSU) is a high-performance thermoplastic known for its exceptional strength, thermal stability, and chemical resistance. It is commonly used in demanding applications, such as in the aerospace, automotive, medical, and electronics industries, where materials must withstand harsh conditions.
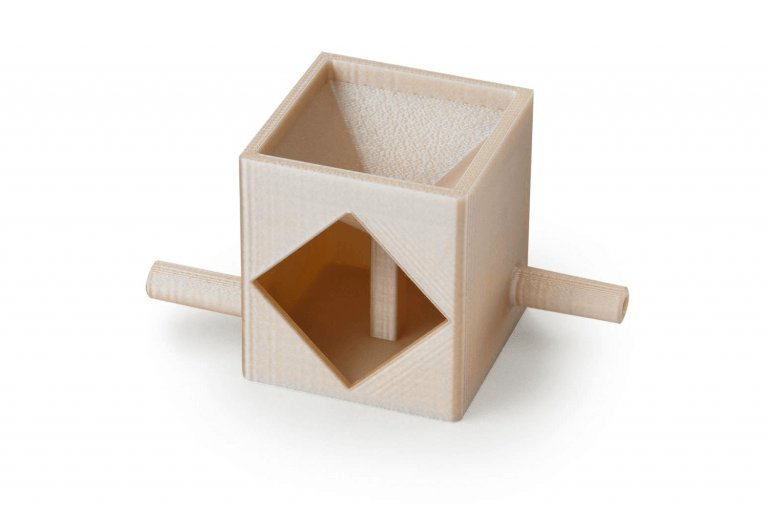
Property | ASTM | Metric Units |
---|---|---|
Tensile Strength | D638M | 55 MPa |
Modulus of Elasticity, Youngs Modulus | D638M | 2,100 MPa |
Elongation at Break (%) | D638M | 3% |
Flexural Strength | D790M | 110 MPa |
Flexural Modulus | D790M | 2,200 MPa |
IZOD Impact (notched) | D256A | 58.7 J/m |
Heat Deflection Temperature at .45 MPa/66 psi (°C) | D648 | 189 °C |
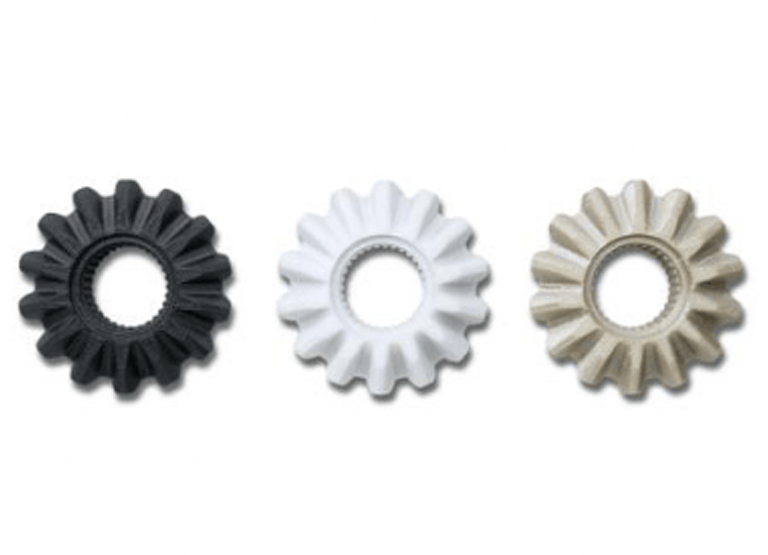