PC-ABS (Polycarbonate-ABS) is a high-performance industrial thermoplastic, widely recognized for its exceptional impact resistance and strength.
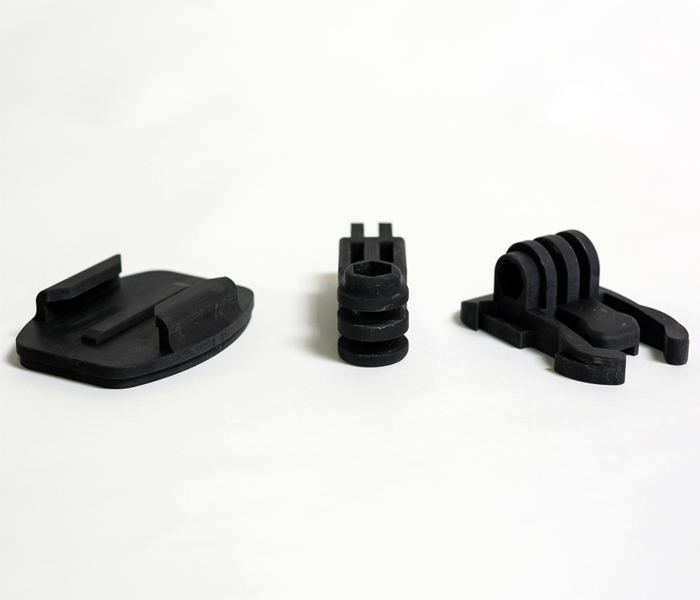
Property | ASTM | Metric Units |
---|---|---|
Tensile Strength | D638M | 41 MPa |
Modulus of Elasticity, Youngs Modulus | D638M | 1,900 MPa |
Elongation at Break (%) | D638M | 6% |
Flexural Strength | D790M | 68 MPa |
Flexural Modulus | D790M | 1,900 MPa |
IZOD Impact (notched) | D256A | 196 J/m |
Heat Deflection Temperature at .45 MPa/66 psi (°C) | D648 | 110 °C |
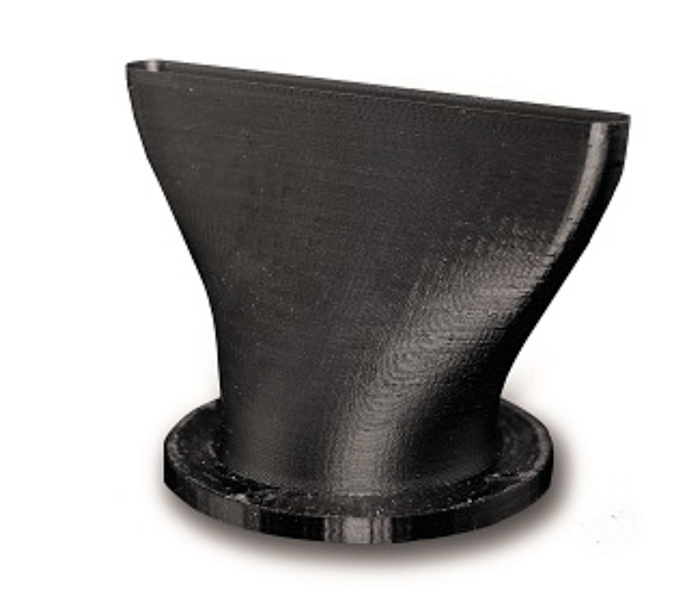