Engineered for applications where strength meets efficiency, lightweight metals provide unmatched versatility across aerospace, automotive, and other performance-driven industries.
Below is an overview of the lightweight metals available and their unique advantages:
Known for their excellent corrosion resistance, machinability, and strength-to-weight ratio.
- Ideal Applications: Aircraft structures, automotive frames, and consumer electronics.
- Unique Characteristics: Highly recyclable and versatile for a wide range of industrial uses.
One of the lightest structural metals available, offering good strength and damping capacity.
- Ideal Applications: Aerospace components, lightweight automotive parts, and electronics casings.
- Unique Characteristics: Superior vibration damping and ease of machining.
Combines high strength with corrosion resistance and low weight.
- Ideal Applications: Aerospace fasteners, medical implants, and high-performance automotive components.
- Unique Characteristics: High biocompatibility and exceptional performance in extreme environments.
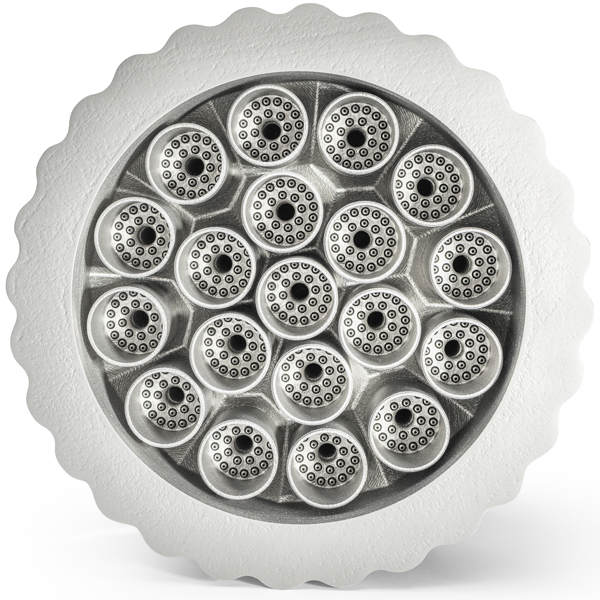
Lightweight metals are specifically engineered to provide the strength of heavier materials while significantly reducing overall mass. This makes them essential in applications where weight reduction directly impacts performance, such as aerospace structures, electric vehicles, and wearable medical devices.
- Why It Matters: Lower weight reduces fuel consumption, increases payload capacity, and enhances maneuverability in transportation and aerospace applications.
- Example: Aluminum alloys used in aircraft wings balance durability and weight reduction, improving flight efficiency.
Many lightweight metals, such as aluminum and titanium, naturally resist corrosion, even in harsh environments. This property minimizes maintenance requirements and extends the operational life of components exposed to moisture, chemicals, or extreme temperatures.
- Why It Matters: Corrosion resistance ensures structural integrity in marine, aerospace, and outdoor industrial applications.
- Example: Magnesium alloys with protective coatings are used in marine electronics to resist saltwater corrosion.
Lightweight metals are easy to shape, cut, and form into complex geometries, making them ideal for precision engineering. Their machinability enables cost-effective production and design flexibility for advanced applications, such as aerospace components and intricate electronics casings.
- Why It Matters: Enables innovation in design, supporting the creation of lightweight yet complex components.
- Example: Aluminum is widely used in die-casting for automotive parts due to its ease of machining and consistency.
Lightweight metals are among the most sustainable materials, with many being infinitely recyclable without losing their properties. This makes them a key resource for eco-conscious manufacturing and circular economies.
- Why It Matters: Reducing reliance on virgin material lowers environmental impact and supports green initiatives.
- Example: Recycled aluminum is used in building materials and consumer goods, maintaining the same quality as new aluminum.
Lightweight metals often feature excellent thermal and electrical conductivity, making them indispensable for managing heat in high-performance electronics and power systems. This characteristic also enhances their functionality in cooling systems, heat exchangers, and power transmission lines.
- Why It Matters: Efficient thermal management improves system reliability and longevity in high-performance applications.
- Example: Aluminum heat sinks are used in LED lighting and electronic devices to dissipate heat effectively.
Lightweight metals are the cornerstone of aerospace innovation, where reducing weight translates directly into fuel efficiency, extended range, and improved payload capacity. Their combination of strength, corrosion resistance, and machinability makes them ideal for critical aerospace components.
- Aircraft Fuselage and Wings: Aluminum alloys are widely used for structural integrity and weight reduction, enhancing fuel efficiency and maneuverability.
- Landing Gear Components: Lightweight metals, like titanium, are used for landing gear to withstand high loads while minimizing added weight.
- Fuel Tanks: Magnesium and aluminum alloys are used in fuel tank construction to reduce weight and optimize fuel storage capacity.
Lightweight metals play a critical role in defense applications, where reducing weight without compromising strength and durability can mean the difference between mission success and failure.
- Lightweight Armor: Aluminum and titanium are used to develop armor plating for vehicles, aircraft, and personal protection, providing effective ballistic resistance with reduced weight.
- Structural Components: Magnesium alloys are utilized in aircraft and ground vehicles to improve mobility and reduce logistical burdens.
In the automotive industry, lightweight metals contribute to more efficient, eco-friendly vehicles by reducing overall vehicle weight without sacrificing safety or performance.
- Lightweight Frames and Engine Components: Aluminum and magnesium alloys reduce vehicle weight, improving fuel efficiency and reducing emissions while maintaining crash safety standards.
- Electric Vehicle (EV) Battery Enclosures: Aluminum enclosures are used to protect EV batteries while providing thermal management to optimize performance and longevity.
In industrial applications, lightweight metals enable efficient designs for equipment and structures that require durability and reduced mass for ease of handling and transport.
- Lightweight Scaffolding: Aluminum scaffolding is preferred for its corrosion resistance and portability, making it ideal for construction and maintenance.
- Rail Systems: Lightweight metals are used in railcars and tracks to improve energy efficiency and reduce wear on infrastructure.
- Manufacturing Equipment: Magnesium and aluminum alloys are used to create lightweight yet strong tooling and fixtures for manufacturing processes, reducing operator fatigue and improving productivity.
As devices become thinner and more powerful, lightweight metals are crucial for balancing durability and portability while ensuring proper heat management.
- Casing for Laptops, Smartphones, and Tablets: Aluminum and magnesium alloys are preferred for their lightweight nature, sleek appearance, and durability against impacts and wear.
- Heat Sinks for Thermal Management: Aluminum’s high thermal conductivity makes it an essential material for heat sinks in laptops, servers, and LED lighting to dissipate heat efficiently and extend component life.
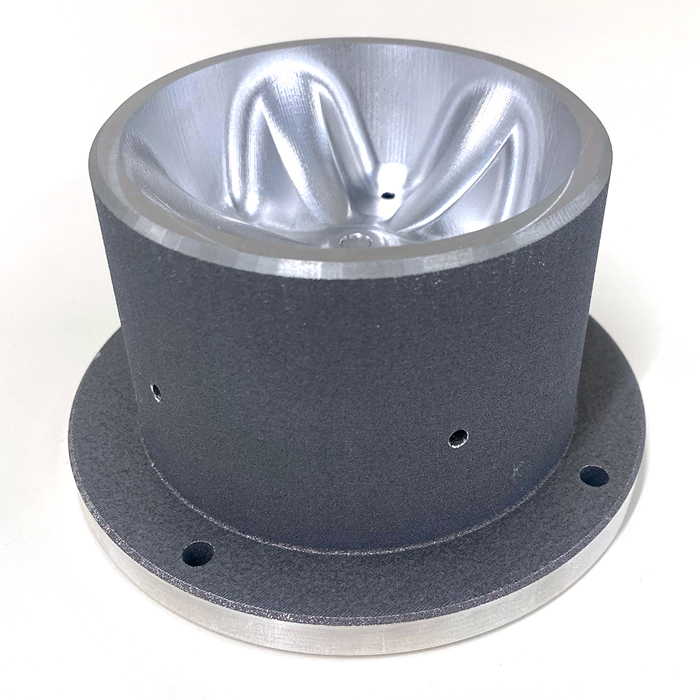