Accelerate Your Launch. Streamline Your Supply Chain. Launching into Earth’s orbit, propelling assets, and protecting them while traveling at hypersonic speeds is possible with our comprehensive manufacturing solutions. Our services range from the development of refractory metal thrusters and nozzles to precision machining of the most difficult materials.
The Sky's Not the Limit
Parts We Produce
Our team produces high quality, commercial space applications for a variety of Tier 1 suppliers across additive and machining production methods.
- In-Space Propulsion Elements
- Satellite Positioning Control & Tug
- RCS (Reaction Control System)
- Lander descent/ascent, abort/escape, and re-entry
- Thermal Protection Systems (TPS) for Re-Entry
- Aero Engine Components (such as those used in rockets and spacecraft)
- Regen Rocket Engines (used in rocket propulsion systems)

Thrusting Ahead
We are transforming space propulsion enhancing satellite operations and complex space maneuvers through our innovations in additive manufacturing. Our specialized approach in metallurgy allows for additive manufacturing of superior refractory alloys, surpassing traditional materials in quality and durability. These developments offer remarkable creep resistance and stability at temperatures above 2,000 degrees Celsius, marking significant advancements in space technology.
- 3D-printed Nb C103 refractory thrusters proven in space
- High mach proven leading edge with integrated cooling
- Mesh with variable density and embedded internal structures
- High-quality, low-cost thrusters, injectors, and hot gas manifolds
- Exceptional strength, impact, creep and oxidation resistance
Report: Additively Manufactured C103 for Propulsion Applications
With melting points above 2,200 degrees C, refractory metals, such as Niobium, are highly heat and corrosion-resistant. Propulsion systems in the upper stage are using Niobium machined from its raw form. This is because it’s traditionally been difficult to 3D print and maintain the material properties needed for hypersonic flight. But through metallurgical control Chief Scientist Youping Gao, Ph.D. 🦕 was able to produce material far superior to the wrought material.
Read Dr. Youping Gao’s scientific contributions in this industry-leading NASA report:
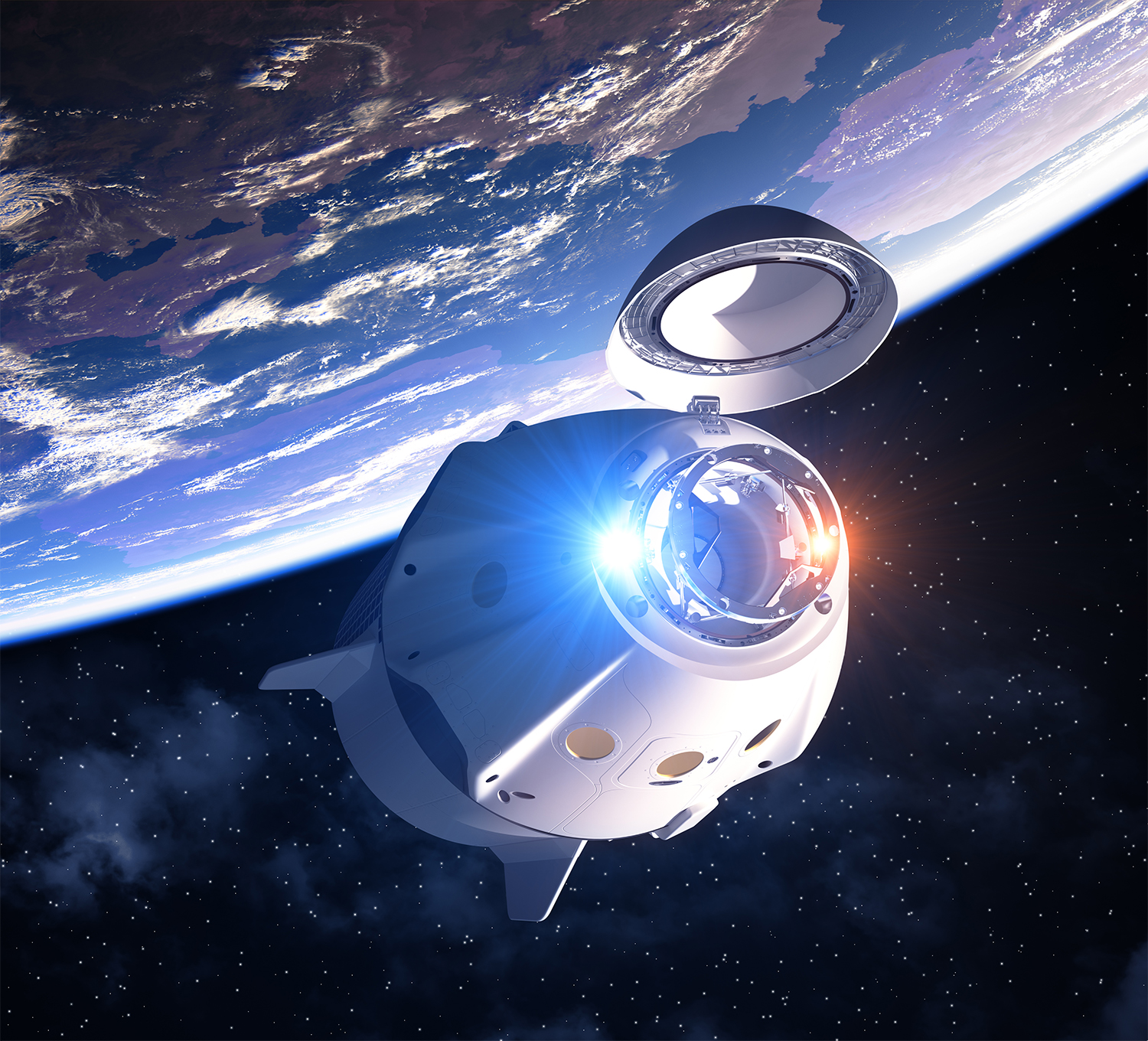
Breaking Down the Business of Commercial Space
In the highly specialized and competitive field of commercial space, companies often break down their businesses into tiers to ensure that each component of their operations is optimized for efficiency and quality.
Tier 1 focuses on the manufacturing of anything that goes into space, such as rockets, satellites, and other space-bound hardware.
Tier 2 is responsible for producing anything that holds these components, such as the containers, tubes, and frames that are necessary for space travel.
Tier 3 is concerned with engineering, including the design and testing of the products produced in Tiers 1 and 2.
Commercial space companies rely on advanced manufacturing technologies like 3D printing and rapid prototyping. These technologies help create intricate molds and prototypes that refine designs and meet the demanding requirements of space exploration.
Common Materials Used for Space Parts
Titanium – Titanium is a lightweight, strong, and corrosion-resistant metal that is used extensively in the aerospace industry, including for the production of rockets, satellites, and aircraft parts. 3D printed titanium parts offer greater design freedom, reduced material waste, and lower production costs.
Inconel 718 – Inconel 718 is a nickel-chromium alloy that is highly resistant to corrosion and oxidation. It is commonly used in the aerospace and defense industries for the production of engine components, rocket motors, and gas turbines. 3D printing allows for more complex geometries and reduced production times compared to traditional manufacturing techniques.
Haynes 230 – Haynes 230 is a nickel-chromium-tungsten-molybdenum alloy that is highly resistant to both oxidizing and reducing environments. It is commonly used in gas turbine engines, industrial furnaces, and heat exchangers. 3D printing can enable the production of highly complex and customized Haynes 230 parts that would be difficult or impossible to manufacture using traditional techniques.
Aluminum – Aluminum is a lightweight and corrosion-resistant metal that is widely used in the aerospace industry for the production of aircraft components and structures.
Niobium – Niobium is a highly conductive metal that is used in the production of superconducting magnets, particle accelerators, and other high-tech applications. 3D printing of niobium parts can enable greater precision and efficiency in these applications.
Ultem – Ultem is a high-performance thermoplastic with excellent strength and heat resistance. Used for aerospace components that require high strength-to-weight ratios, such as structural components, housings, and electrical connectors.
PEEK – Peek is a high-performance thermoplastic with excellent mechanical properties and chemical resistance. Used for parts that require high strength, stiffness, and dimensional stability, such as turbine components and rocket engine parts.
PEI – PEI is a high-performance thermoplastic with excellent strength and chemical resistance. Used for parts that require high temperature resistance and dimensional stability, such as heat shields and engine components.
TPU – TPU is a flexible thermoplastic used for applications that require shock absorption and vibration damping, such as landing gear components and vibration isolators.