Design Guidelines for Conformal Cooling Channels in Metal 3D Printed Components
In metal 3D printing, the integration of conformal cooling channels can significantly enhance the performance and efficiency of printed components. By optimizing the design of these channels, engineers can achieve improved heat transfer, reduced cycle times, and enhanced part quality. This blog post presents essential design guidelines for incorporating conformal cooling channels in metal 3D printed parts, covering key considerations and the importance of simulation and analysis tools.
Channel Placement
Effective channel placement is an important aspect of designing conformal cooling channels in metal 3D-printed components. It involves strategically determining the optimal locations for the channels to maximize cooling efficiency while considering the geometry of the part, heat distribution patterns, and critical cooling areas.
One key consideration is to identify regions of the part that experience high heat accumulation or are prone to thermal distortions. These areas may require a higher density of cooling channels to dissipate heat effectively and mitigate potential defects. Additionally, channel placement should aim to provide uniform cooling throughout the part to ensure consistent material properties and minimize residual stresses.
However, careful attention must be paid to avoid interference with other design elements or potential issues during the printing process. Channel placement should consider accessibility for powder removal in powder bed fusion processes and proper support structures in other metal 3D printing techniques. By striking the right balance between optimal cooling and design constraints, engineers can achieve an efficient channel placement strategy that maximizes the cooling performance of the metal 3D-printed components.
Shape Optimization
Shape optimization also plays a critical role in designing conformal cooling channels for metal parts. The shape of the channels can significantly impact the cooling performance and overall integrity of the part. Engineers should explore different channel cross-sections, such as circular, rectangular, serpentine, or customized geometries, to determine the most suitable shape for their specific application.
The choice of channel shape influences fluid flow characteristics, pressure drop, and heat transfer efficiency. While circular channels offer simplicity and ease of manufacture, alternative shapes can provide enhanced heat dissipation by promoting increased fluid turbulence and extending the contact area with the surrounding material.
Moreover, complex and curved channel geometries can conform precisely to the part’s shape, maximizing the contact surface area and improving heat transfer. Utilizing these intricate geometries enables efficient cooling of intricate features, corners, and challenging-to-reach areas, which may be prone to overheating or warping during the manufacturing process.
To optimize shape design, engineers can leverage advanced CAD software and simulation tools. These tools allow for virtual testing and evaluation of various channel geometries, facilitating the selection of the most efficient shape based on heat transfer simulations, fluid dynamics analysis, and overall part performance considerations. By strategically optimizing the shape of conformal cooling channels, engineers can achieve enhanced cooling capabilities, reduced thermal gradients, and improved dimensional stability in metal 3D-printed components.
Simulation and Analysis Tools
Simulation and analysis tools are vital for designing and optimizing conformal cooling channels in metal 3D-printed components. These tools provide valuable insights into fluid flow, heat transfer, and thermomechanical behavior, enabling informed design decisions and performance predictions.
With advanced software packages, engineers can create virtual models of their parts with integrated conformal cooling channels, allowing for simulations of fluid flow and heat transfer. Computational fluid dynamics (CFD) simulations help optimize channel designs, assess flow rates, and ensure uniform cooling and efficient heat dissipation. Thermal analysis tools predict temperature gradients, evaluate cooling strategies, and minimize thermal stresses and distortion.
By integrating simulation and analysis tools, engineers refine cooling channel designs, reduce physical prototyping, and achieve optimized cooling performance in metal 3D-printed components with confidence and precision.
Material Selection
The choice of materials for both the metal 3D printed components and the conformal cooling channels is crucial for effective cooling and overall performance. At ADDMAN, with our expertise in thermal management and specialization in complex materials like refractories, we understand the significance of material selection in achieving optimal cooling capabilities.
When selecting materials for conformal cooling channels, several factors come into play. First, thermal conductivity is a critical consideration as it determines the channel’s ability to transfer heat efficiently. Materials with high thermal conductivity, such as copper or aluminum alloys, are often preferred for their excellent heat dissipation properties.
Additionally, compatibility with the metal 3D printing process is essential. The material selected for the cooling channels should be compatible with the printing technique used, ensuring successful fabrication and integration without compromising the part’s structural integrity.
Moreover, resistance to thermal cycling and corrosion is vital, especially in applications with repeated heating and cooling cycles. The material should withstand the thermal stresses and potential chemical reactions that may occur during the cooling process.
In complex applications where specialized materials like refractories are required, such as high-temperature environments or challenging materials, expertise in material selection becomes paramount. Our team at ADDMAN is well-versed in working with complex materials, including refractories, to provide tailored solutions for effective thermal management in metal 3D-printed components.
By carefully considering the thermal properties, compatibility, and resistance to thermal cycling and corrosion, engineers can select the most appropriate materials for both the metal 3D printed components and the conformal cooling channels. This ensures optimal cooling performance, improved part quality, and enhanced thermal management in challenging applications.
Overcoming Design Constraints
When incorporating conformal cooling channels in metal 3D printed components, engineers must address various design constraints to achieve successful implementation. These constraints may arise from the printing process itself, accessibility for powder removal in powder bed fusion, or the need to accommodate post-processing requirements. At ADDMAN, we are experienced in navigating these challenges to optimize conformal cooling designs without compromising efficiency.
Printer resolution and limitations may impose constraints on channel dimensions, such as minimum feature sizes or aspect ratios. Design modifications, such as adjusting channel diameters or optimizing channel layouts, can help overcome these constraints while still ensuring effective cooling performance.
Accessibility for powder removal is crucial in powder bed fusion processes. Proper consideration should be given to the design of channels to allow for efficient powder removal, avoiding blockages and ensuring the channels are free from residual powder.
Post-processing requirements, such as heat treatment or surface finishing, may affect the design and integration of cooling channels. Engineers must account for these processes and plan the channel layout accordingly, allowing for proper access and maintaining the desired part properties.
By proactively addressing these design constraints, engineers can optimize the conformal cooling channel design without compromising cooling efficiency. At ADDMAN, our expertise in metal 3D printing allows us to find innovative solutions, ensuring effective cooling while accommodating the unique constraints of each application.
Closing Thoughts
Designing effective conformal cooling channels in metal 3D printed components requires careful consideration of channel placement, shape optimization, heat transfer principles, and the use of simulation and analysis tools. By following these design guidelines, engineers can achieve optimal cooling performance, reduced cycle times, and improved part quality in metal 3D printing applications. Implementing conformal cooling channels unlocks new possibilities for producing complex, high-performance components with enhanced functionality and durability.
For more information check out this video series courtesy of 3D Systems:
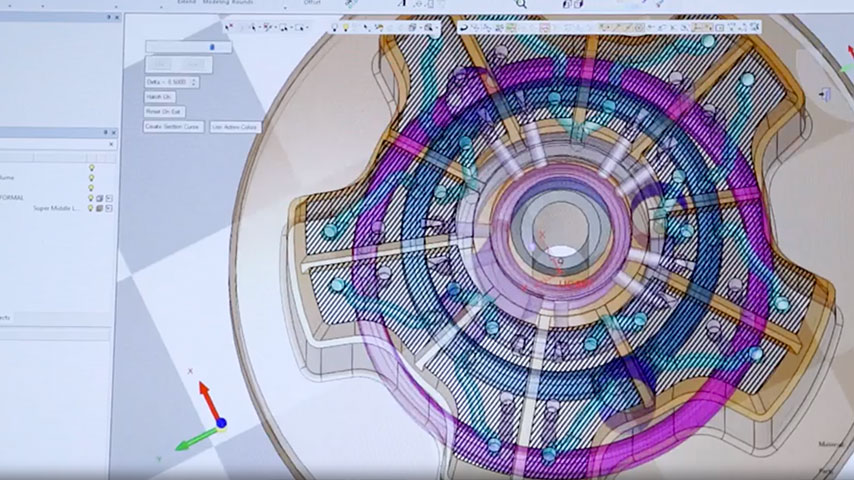