Nylon materials deliver exceptional strength, flexibility, and wear resistance, making them ideal for 3D printing and manufacturing in industries like automotive, aerospace, and consumer goods.
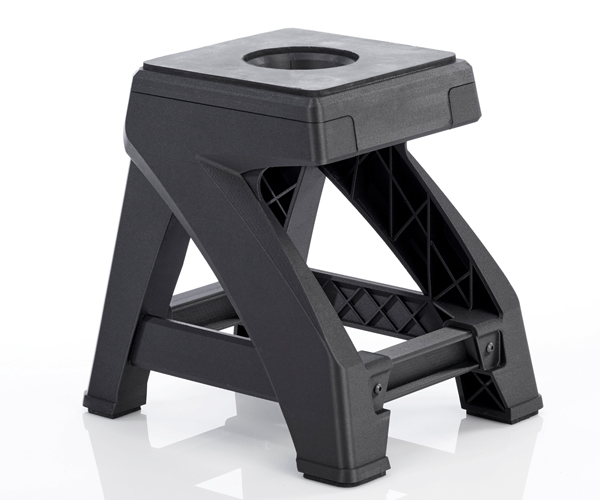
Below is an overview of the nylons available and their unique advantages:
A durable, lightweight material with low moisture absorption and high chemical resistance.
- Ideal Applications: Automotive brackets, industrial fixtures, and precision prototypes.
- Unique Characteristics: Dimensional stability and impact resistance for high-performance parts.
A tough, strong nylon with excellent thermal and mechanical properties.
- Ideal Applications: Gears, bushings, and load-bearing components.
- Unique Characteristics: Superior wear resistance and durability under continuous stress.
A Multi Jet Fusion (MJF) material offering precise detailing and excellent surface finishes.
- Ideal Applications: Medical device housings, lightweight enclosures, and consumer products.
- Unique Characteristics: High-resolution printing capabilities with a clean, professional aesthetic.
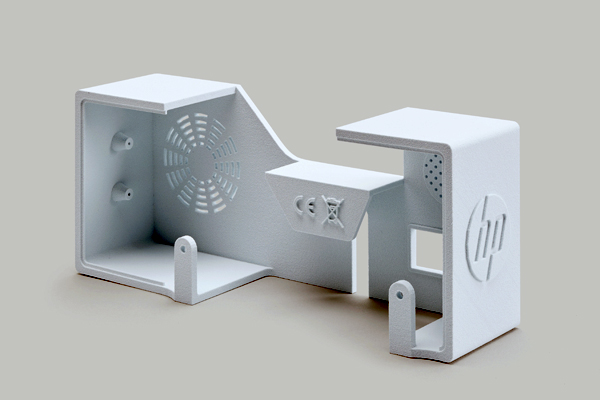
Nylon materials are renowned for their ability to deliver excellent tensile strength and impact resistance, making them ideal for use in high-stress and load-bearing applications. Their mechanical properties enable parts to withstand heavy use and resist deformation under pressure, ensuring long-term reliability and performance.
- Why It Matters: Strength and durability are critical for functional components that must endure repeated mechanical stress or harsh operational environments. Nylon’s properties reduce the likelihood of breakage, prolonging product life and enhancing safety.
- Applications:
- Automotive gears and bushings that resist wear under continuous motion.
- Structural aerospace brackets that must withstand high loads during flight.
- Industrial conveyor components exposed to repetitive mechanical stress.
Unlike many other polymers, nylon materials like Nylon 12 exhibit low moisture absorption, which preserves dimensional stability even in humid environments. This property ensures that parts maintain their size, shape, and functionality, regardless of exposure to moisture.
- Why It Matters: Moisture absorption can compromise part performance, causing swelling or warping that leads to misalignment or failure. Low-moisture-absorption nylons are ideal for precision parts used in variable environmental conditions.
- Applications:
- Outdoor consumer products such as electronic housings or sporting goods.
- Medical diagnostic equipment operating in high-humidity environments.
- Industrial components that maintain performance in fluctuating environmental conditions.
Nylon materials perform reliably in high-temperature environments, withstanding prolonged exposure to elevated operating temperatures without losing their mechanical properties. This makes them suitable for applications where heat resistance is essential.
- Why It Matters: Components exposed to high temperatures often degrade or lose strength over time. Nylon’s ability to retain structural integrity at elevated temperatures ensures reliability in heat-intensive applications.
- Applications:
- Automotive engine components exposed to extreme heat.
- Aerospace parts, such as ducts and enclosures, that must endure high-temperature conditions during operation.
- Industrial tooling and fixtures used in heated manufacturing processes.
Nylon is widely utilized in aerospace for lightweight and durable components that perform under extreme conditions. Its thermal stability and precision printing capabilities make it perfect for advanced engineering needs.
- Lightweight Enclosures and Durable Fixtures for Structural Components
Aerospace applications benefit from nylon’s combination of low weight and high strength, reducing overall aircraft weight while maintaining durability.Examples: Electrical enclosures, protective housings, and structural supports. - Jigs and Prototypes for Aerospace Engineering Applications
Nylon is frequently used to create high-precision jigs, fixtures, and prototypes for testing and assembly in aerospace manufacturing.Examples: Assembly guides, alignment jigs, and wind tunnel test models.
Nylon’s biocompatibility, sterilization compatibility, and lightweight properties make it highly suitable for medical applications. These materials are used to create functional, reliable components for healthcare equipment.
- Sterilizable Housings and Lightweight Components for Diagnostic Equipment
Nylon’s chemical resistance and ability to withstand repeated sterilization make it ideal for durable medical device housings.Examples: Enclosures for diagnostic machines, portable medical device cases, and monitoring equipment. - Functional Prototypes for Surgical Tools and Custom Guides
Nylon is commonly used for prototyping surgical instruments and creating custom surgical guides that require precise detailing and durability.Examples: Bone cutting guides, alignment tools, and trial implants for surgical procedures.
Nylon materials are indispensable in the automotive industry due to their strength, durability, and ability to withstand mechanical stress. These materials are widely used for lightweight, high-performance components that enhance vehicle efficiency and reliability.
- Durable Brackets, Clips, and Lightweight Structural Components
Nylon’s strength-to-weight ratio makes it ideal for producing lightweight yet strong components, reducing vehicle weight while maintaining structural integrity.Examples: Engine brackets, dashboard clips, and lightweight mounting systems. - High-Performance Gears and Bushings for Engine Systems
Nylon’s wear resistance and ability to withstand friction make it ideal for gears and bushings that operate under continuous mechanical stress.Examples: Timing gears, engine mounts, and suspension bushings.
Nylon materials excel in industrial applications where components must endure heavy loads, repetitive motion, and harsh environments. Their chemical resistance and durability make them a preferred choice for demanding manufacturing processes.
- Machine Bushings, Conveyor Components, and Tooling for Heavy-Duty Manufacturing
Nylon’s wear resistance and ability to handle high-stress conditions ensure reliability in industrial machinery and equipment.Examples: Conveyor rollers, custom bushings, and machine guards. - Durable Fixtures and Custom Tooling for Precision Processes
Nylon parts provide the accuracy and durability needed for tooling and fixtures in high-precision manufacturing workflows.Examples: Clamps, fixtures for CNC machining, and assembly tools.
Nylon is a popular material in consumer goods due to its durability, flexibility, and ability to deliver high-quality finishes. It enhances the functionality and longevity of everyday products.
- Wear-Resistant Cases, Grips, and Sporting Goods
Nylon’s strength and resistance to wear make it ideal for products that experience frequent handling or impact.Examples: Smartphone cases, ergonomic grips, and durable sports equipment. - High-Quality Enclosures for Electronics and Household Items
Nylon’s ability to produce smooth surface finishes and intricate details is perfect for creating aesthetically pleasing and functional enclosures.Examples: Electronic device housings, remote controls, and kitchen appliances.