Polyurethane-based polymers combine flexibility, durability, and chemical resistance, making them indispensable for a wide range of industries, including automotive, medical, consumer goods, and industrial applications.
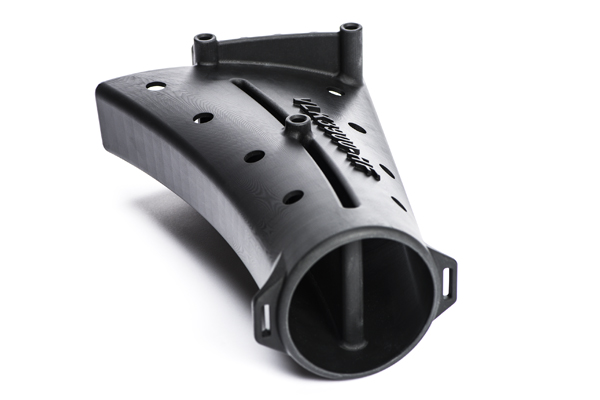
Below is an overview of the polyurethane-based polymers available and their unique advantages:
A flexible material designed for 3D printing applications requiring elasticity and wear resistance.
- Ideal Applications: Snap-fit parts, enclosures, and cushioning components.
- Key Features: High impact resistance, flexibility, and durability in dynamic environments.
A rigid material with exceptional thermal stability and mechanical strength.
- Ideal Applications: Structural components, fixtures, and lightweight industrial parts.
- Key Features: Excellent strength-to-weight ratio and resistance to heat and chemicals.
A high-performance rigid material offering exceptional durability and environmental stability.
- Ideal Applications: Automotive components, durable enclosures, and end-use parts.
- Key Features: Superior thermal resistance and toughness, suitable for heavy-duty applications.
A medical-grade polyurethane suitable for biocompatible and sterilizable parts.
- Ideal Applications: Medical devices, surgical guides, and diagnostic equipment housings.
- Key Features: Certified for biocompatibility, capable of withstanding sterilization processes.
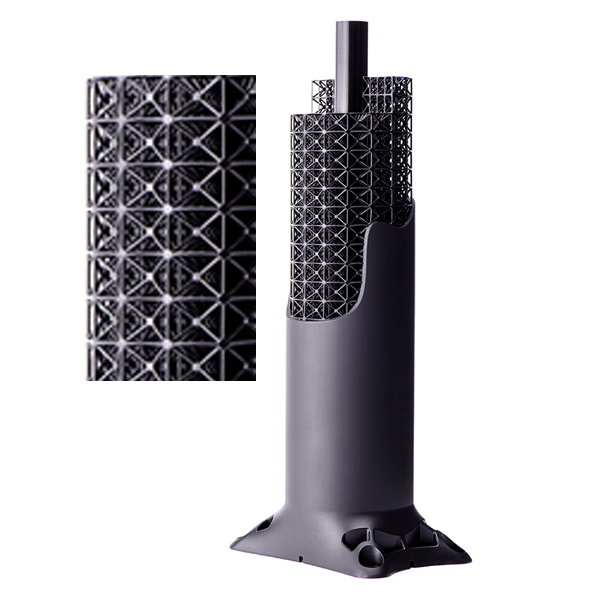
Polyurethane-based materials are designed to absorb and dissipate energy during impacts, providing excellent durability and shock absorption. These properties make them essential for dynamic and high-stress environments, where components must endure repeated or sudden forces without cracking or breaking.
- Why It Matters: High impact resistance extends the lifespan of components and ensures reliability in demanding applications like vibration dampeners, machine parts, and protective gear.
- Applications:
- Vibration dampeners in industrial machinery reduce wear caused by continuous motion.
- Footwear components such as midsoles and outsoles provide cushioning and durability.
- Automotive parts like engine mounts and shock absorbers enhance performance and safety.
Polyurethane materials are available in a wide range of formulations, offering both flexible elastomers and rigid resins to meet diverse needs. Their ability to provide structural strength or elasticity ensures suitability for a variety of stress levels and environmental conditions.
- Why It Matters: This versatility allows manufacturers to use polyurethane materials for a broad spectrum of applications, from creating soft, elastic components to producing rigid, load-bearing structures.
- Applications:
- Rigid polyurethane foams for lightweight enclosures and structural supports.
- Flexible TPU components for wearable devices and snap-fit parts.
- Elastomers for seals, rollers, and industrial parts requiring flexibility.
Polyurethane-based materials are highly resistant to chemical exposure, oils, solvents, and high temperatures. They remain stable under extreme conditions, making them ideal for harsh operating environments in industrial, automotive, and medical settings.
- Why It Matters: Resistance to chemicals and heat minimizes degradation over time, ensuring consistent performance and reducing maintenance. This is crucial for industrial machinery, automotive parts, and medical devices that operate in chemically aggressive or high-temperature environments.
- Applications:
- Conveyor belts in manufacturing withstand industrial oils and cleaning agents.
- Automotive seals and gaskets resist engine fluids and high temperatures.
- Medical diagnostic tools endure repeated sterilization without losing integrity.
Polyurethane materials combine low weight with high mechanical strength, enabling reduced overall product weight without compromising performance. This is particularly valuable in industries where weight reduction directly impacts efficiency, such as aerospace, automotive, and wearable technology.
- Why It Matters: Lightweight materials improve mobility, fuel efficiency, and ease of handling, while durability ensures long-term reliability even in high-stress environments.
- Applications:
- Lightweight panels for automotive and aerospace components reduce fuel consumption and improve performance.
- Wearable medical devices benefit from lightweight, comfortable materials with durability.
- Portable electronics gain added durability without increased bulk.
Polyurethane-based materials play a critical role in the automotive industry, offering lightweight durability, vibration dampening, and impact resistance. These properties are essential for improving vehicle performance, fuel efficiency, and passenger comfort.
- Lightweight Structural Parts, Brackets, and Mounts
Polyurethane components reduce overall vehicle weight while maintaining strength and stability. This contributes to increased fuel efficiency and enhanced structural integrity.- Examples: Lightweight brackets for engine compartments and interior mounts for dashboards.
- Vibration Dampening Components for Improved Durability
Polyurethane absorbs and reduces vibration from engines, road conditions, and mechanical systems, improving vehicle lifespan and passenger comfort.- Examples: Engine mounts, suspension bushings, and shock-absorbing pads.
Polyurethane’s chemical resistance, durability, and ability to withstand sterilization make it ideal for medical applications. These materials are commonly used in devices that require precision, sterility, and biocompatibility.
- Sterilizable Surgical Guides and Housings for Diagnostic Tools
Polyurethane materials are compatible with autoclave and chemical sterilization processes, ensuring safe reuse without degradation.- Examples: Surgical cutting guides, medical imaging tool housings, and diagnostic device enclosures.
- Biocompatible Components for Portable Medical Equipment
Lightweight and durable, polyurethane-based parts are used in portable diagnostic and treatment devices that demand comfort and reliability.- Examples: Wearable monitoring device casings and flexible tubing connectors.
In industrial settings, polyurethane materials excel in heavy-duty applications requiring abrasion resistance, impact absorption, and durability under stress.
- Custom Rollers, Vibration Dampeners, and Heavy-Duty Machine Bushings
Polyurethane is ideal for components that endure continuous movement and mechanical stress, reducing wear and prolonging equipment life.- Examples: Conveyor belt rollers, vibration isolators, and industrial machine bushings.
- Rigid Enclosures and Durable Fixtures for Manufacturing Equipment
Polyurethane’s rigidity and impact resistance make it perfect for creating long-lasting enclosures and fixtures used in high-volume manufacturing environments.- Examples: Protective equipment housings and tool fixtures for assembly lines.
Polyurethane-based materials are essential in consumer goods, offering flexibility, durability, and impact resistance. These materials enhance the usability and longevity of everyday products.
- Flexible Cases, Grips, and Wearables
Polyurethane provides elasticity and comfort, making it a preferred material for personal-use products requiring ergonomic designs.- Examples: Smartphone cases, fitness trackers, and sports gear.
- Impact-Resistant Parts for Electronics and Household Items
Durable and shock-resistant, polyurethane materials protect electronics and other consumer goods from accidental damage.- Examples: Tablet casings, remote control housings, and durable household tools.
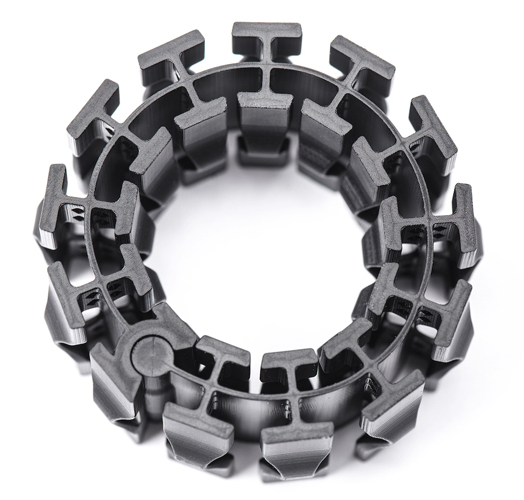