Designed for extreme environments, nickel-based alloys deliver exceptional performance in high-temperature, high-stress, and highly corrosive conditions across aerospace, energy, chemical processing, and marine industries.
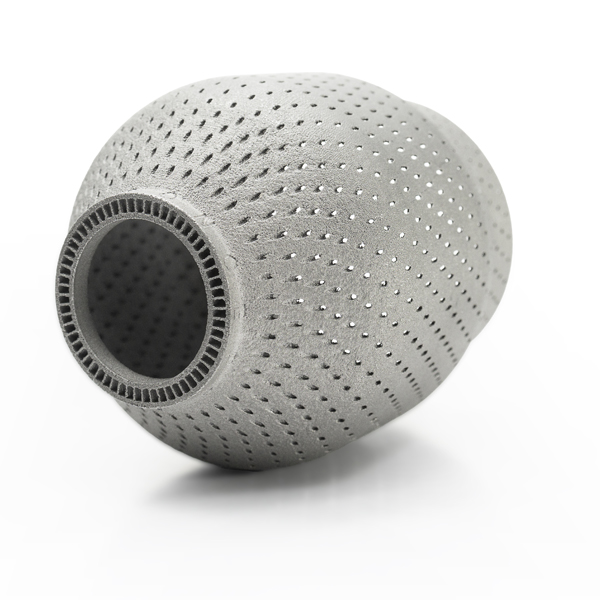
Below is an overview of the nickel alloys available and their unique advantages:
A high-performance, oxidation- and corrosion-resistant alloy designed for extreme heat and mechanical stress.
- Ideal Applications: Jet engines, exhaust systems, gas turbines, and heat exchangers.
- Unique Characteristics: Retains strength at temperatures exceeding 1,000°C, resisting thermal fatigue and oxidation.
Highly resistant to corrosion, particularly in acidic and high-temperature chemical environments.
- Ideal Applications: Chemical reactors, heat exchangers, scrubbers, and marine applications.
- Unique Characteristics: Exceptional resistance to pitting, stress corrosion cracking, and oxidation in aggressive chemical environments.
A durable, corrosion-resistant alloy with excellent mechanical properties, particularly in marine environments.
- Ideal Applications: Shipbuilding, offshore oil rigs, pump and valve components, and aerospace fuel tanks.
- Unique Characteristics: High resistance to seawater corrosion and biofouling, making it ideal for marine and chemical processing applications.
Alloys with controlled thermal expansion properties, designed for precision applications.
- Ideal Applications: Aerospace sensors, cryogenic storage, electronic components, and optical instruments.
- Unique Characteristics: Minimal expansion under temperature changes, ensuring dimensional stability in precision engineering.
High-strength alloys engineered for extreme heat and mechanical loads, often used in aerospace and power generation.
- Ideal Applications: Turbine blades, rocket engine components, and nuclear reactors.
- Unique Characteristics: Superior creep resistance and thermal stability under continuous stress.
Nickel alloys are engineered to perform under extreme temperatures exceeding 1,000°C (1,832°F) without losing structural integrity. Their ability to resist thermal expansion, oxidation, and mechanical stress makes them indispensable in high-heat applications such as jet engines, gas turbines, and rocket propulsion systems.
- Why It Matters: High-temperature environments cause most metals to weaken, deform, or oxidize. Nickel alloys maintain their strength, stability, and functionality, ensuring safe and efficient operation in aerospace, power generation, and industrial furnaces.
- Applications:
- Inconel turbine blades withstand extreme combustion temperatures in jet engines and power plants.
- Nickel superalloys in rocket nozzles allow spacecraft to endure extreme heat and atmospheric reentry.
- Industrial furnaces use nickel alloys for heat shields and high-temperature-resistant parts.
Nickel alloys are highly resistant to corrosion, oxidation, and chemical attack, even in aggressive environments. They perform well in applications exposed to saltwater, acidic solutions, and high-temperature oxidizing conditions, making them ideal for marine, chemical processing, and energy applications.
- Why It Matters: Corrosion shortens the lifespan of components, leading to increased maintenance costs and system failures. Nickel alloys reduce wear and extend operational life, particularly in environments where exposure to moisture, chemicals, and extreme temperatures is unavoidable.
- Applications:
- Hastelloy reactors and pipes in chemical plants resist acid corrosion.
- Monel seawater piping and ship propellers endure constant saltwater exposure.
- Nickel alloy heat exchangers operate in highly acidic or alkaline industrial processes.
Copper alloys maintain excellent mechanical properties over time, resisting deformation, fatigue, and mechanical stress, even in extreme conditions. Some alloys, such as beryllium copper, offer tensile strengths comparable to steel, making them ideal for applications requiring both conductivity and durability.
- Why It Matters: Enhances the longevity of components in high-load and high-wear environments.
- Applications: Bearings, bushings, aerospace components, and high-performance industrial machinery.
- Example: Aluminum bronze is used in heavy machinery and aerospace due to its superior wear resistance and high strength, outperforming traditional bronze and brass.
Nickel alloys provide high tensile strength, impact resistance, and long-term durability, making them ideal for high-stress applications where failure is not an option. These alloys maintain mechanical integrity under extreme conditions, including high pressures, repeated thermal cycling, and mechanical loads.
- Why It Matters: In industries like defense, aerospace, and nuclear energy, materials must withstand intense mechanical forces and pressure differentials. Nickel alloys provide reliability and structural integrity, ensuring safe operation in mission-critical systems.
- Applications:
- Jet engine and aerospace fasteners need extreme strength to endure high G-forces.
- Nuclear reactor components require durability under constant radiation exposure.
- Offshore drilling rigs depend on nickel alloy parts for extreme pressure resistance.
Creep occurs when a material gradually deforms under constant mechanical stress at high temperatures, while fatigue results from repeated cyclic loading over time. Nickel alloys are designed to resist both creep and fatigue, ensuring long-term performance in energy, aerospace, and manufacturing.
- Why It Matters: Creep failure in turbines, aircraft engines, or industrial furnaces can be catastrophic, leading to expensive downtime, equipment failure, or safety hazards. Nickel alloys extend component lifespan and reduce maintenance costs by withstanding prolonged mechanical and thermal stress.
- Applications:
- Power plant turbines operate under extreme mechanical loads and must resist creep over decades.
- Aircraft turbine blades experience continuous high-speed rotation and must resist fatigue.
- Cryogenic storage tanks use nickel alloys to handle thermal expansion and contraction without cracking.
Nickel alloys can be tailored to meet specific application requirements by adjusting their composition. By varying elements like chromium, molybdenum, iron, and cobalt, these alloys can be optimized for heat resistance, corrosion protection, wear resistance, and mechanical strength.
- Why It Matters: Industries demand specialized solutions—whether it’s a nickel alloy that resists sulfuric acid in a refinery or a superalloy that can handle Mach 5+ speeds in a hypersonic missile. Custom formulations provide enhanced performance for unique engineering challenges.
- Applications:
- Nickel-chromium alloys like Inconel for high-temperature aerospace applications.
- Nickel-molybdenum alloys like Hastelloy for corrosion-resistant chemical processing.
- Nickel-iron alloys like Invar for precision instruments with minimal thermal expansion.
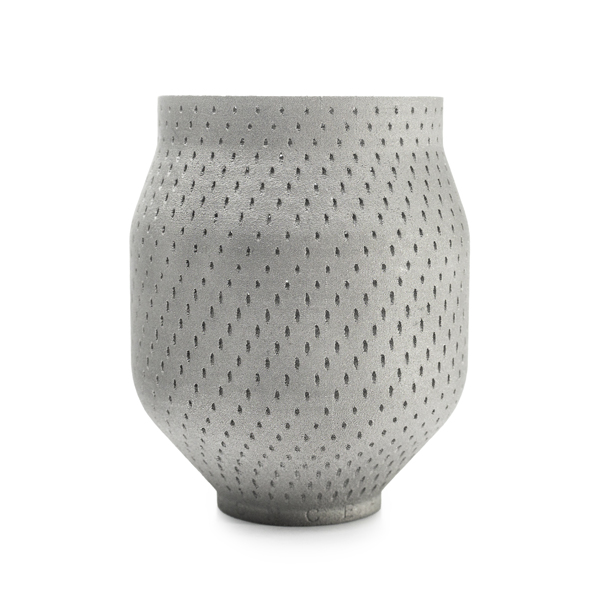