Our comprehensive range of post-processing services is designed to refine, enhance, and prepare your parts for optimal performance, durability, and aesthetics.
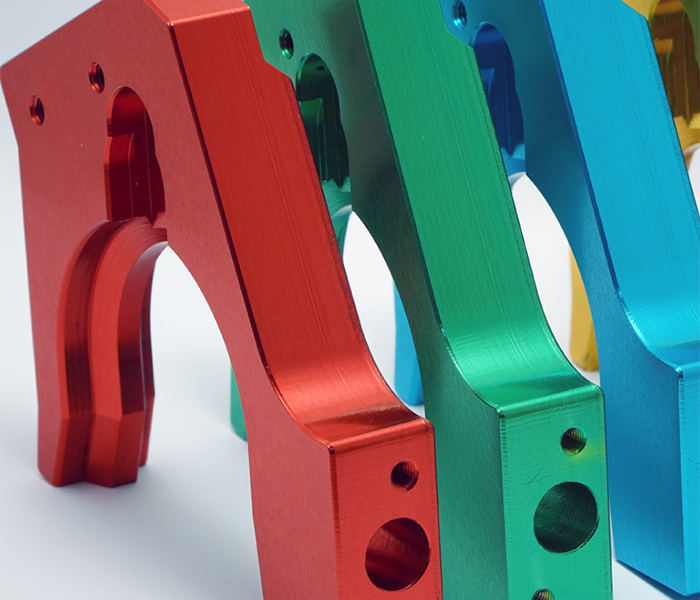
From the first cut to the final finish, we offer a full spectrum of post-processing solutions tailored to meet the unique needs of your project. Our services include:
- Anodizing: Titanium, teflon, sulfuric acid, and hard chrome finishes.
- Polishing & Electropolishing: Smooth, mirror-like surfaces with improved corrosion resistance.
- Powder Coating & Painting: Durable finishes for protection and visual appeal.
- Plating: Zinc, chromium, nickel, copper, and gold for enhanced durability and conductivity.
- Passivation & Chemfilm: Corrosion resistance treatments for stainless steel and other materials.
- Shot Peening & Heat Treating: Strengthen parts and improve fatigue resistance.
- Annealing, Isothermal, & Stress Relief: Optimize material properties for performance-critical applications. Read Blog
- Metal Additive Parts:
Our team of specialists is equipped to machine complex geometries created through metal additive manufacturing. From tight tolerances to smooth finishes, we ensure your components are production-ready with optimal performance. Read Press Release - Polymer Additive Parts:
With advanced CNC machining capabilities, we transform polymer additive parts into high-quality components that match the precision and surface finish of traditional methods like injection molding.
We provide a wide range of post-processing services, both in-house and through trusted partners, to enhance the performance, durability, and appearance of manufactured parts.
Protective and decorative coating for metals, including titanium, teflon-based finishes, and hard chrome using sulfuric acid.
Heat treatments to improve material properties like hardness and durability.
Abrasive cleaning method for surface preparation or achieving a matte finish. Read Blog
Surface conversion for steel and other metals, providing corrosion resistance and a sleek, black finish.
Provides corrosion resistance and prepares surfaces for paint adhesion. Read Blog
Thin, lubricative coatings that reduce friction and wear on parts.
Processes to enhance material strength, durability, and performance.
Application of protective coatings to reduce friction and enhance performance.
Protects specific areas during finishing processes or creates unique visual effects.
Ensures part integrity without causing damage, ideal for quality assurance. Read Blog
Use of nitric or citric acid to remove contaminants and enhance corrosion resistance on stainless steel.
Dye-based method to detect surface defects in materials.
Removes impurities and prepares surfaces for finishing or storage.
Metal coatings such as zinc, chromium, nickel, copper, and gold to improve wear resistance, corrosion protection, and conductivity.
Creates a smooth, high-gloss finish while improving corrosion resistance.
Durable, high-quality finishes applied electrostatically and cured for enhanced surface protection.
Adds protective coatings or aesthetic finishes for various applications.
Strengthening process that improves fatigue life and resistance to cracking by introducing residual compressive stress.
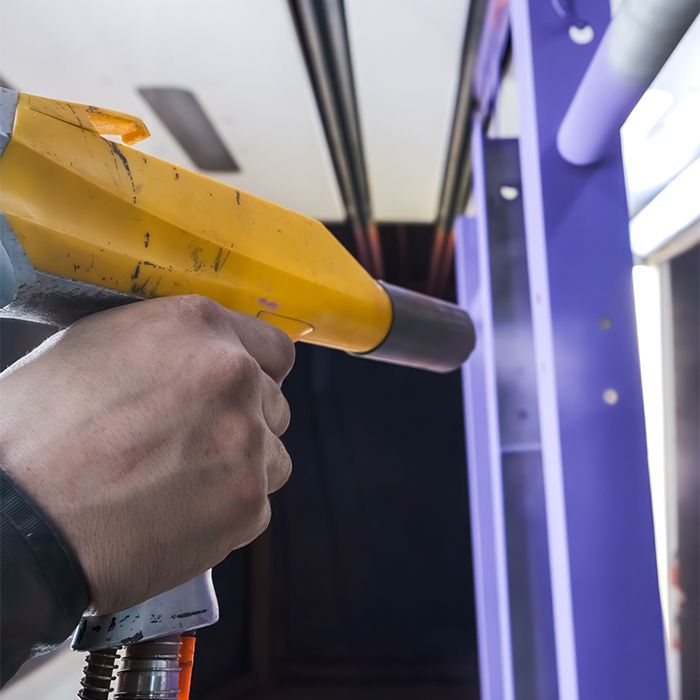
Why Post-Processing Services Are Essential for Manufactured Parts
Post-processing is a critical step in manufacturing that transforms raw or near-finished components into polished, functional, and application-ready parts, ensuring they meet and exceed performance and quality expectations. This indispensable process enhances modern manufacturing workflows in several key ways:
- Removes imperfections like tool marks, layer lines (in additive manufacturing), or rough surfaces.
- Achieves smooth finishes for aesthetic appeal or functional requirements like reduced friction or improved sealing.
- Strengthens parts through treatments like shot peening or heat treating, increasing resistance to wear and fatigue.
- Adds protective coatings (e.g., anodizing, powder coating) to shield against corrosion, chemical exposure, or environmental damage.
- Fine-tunes tolerances to meet exacting specifications, ensuring components fit and function as intended.
- Addresses minor deviations from the manufacturing process for improved consistency.
- Adds essential features like threads, holes, or chamfers that couldn’t be achieved in the primary manufacturing process.
- Customizes parts for specific applications, such as adding lubrication, passivation, or specialized coatings.
- Ensures parts meet the stringent quality, safety, and regulatory requirements of industries like aerospace, medical, and defense.
- Validates integrity through non-destructive testing (NDT) or other inspection processes.
- Enhances the visual quality of parts, making them market-ready for consumer-facing or high-profile applications.
- Adds branding or decorative finishes, such as polished or anodized surfaces.
- Reduces maintenance costs by improving durability and resistance to wear.
- Extends the lifespan of components, reducing the need for frequent replacements.