Our advanced milling capabilities empower industries to produce complex geometries, achieve tight tolerances, and scale production seamlessly—all while maintaining the highest quality standards.

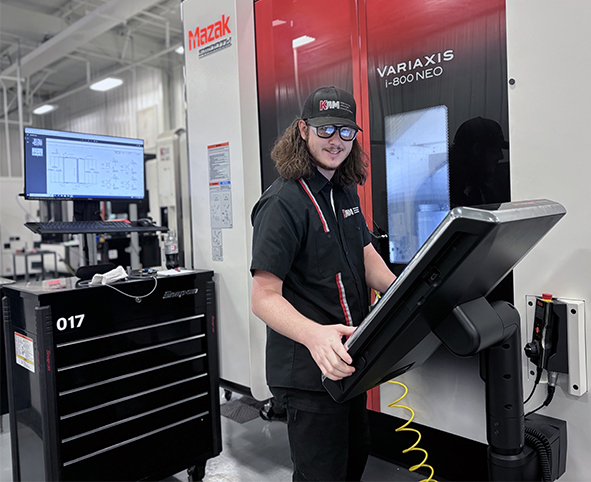
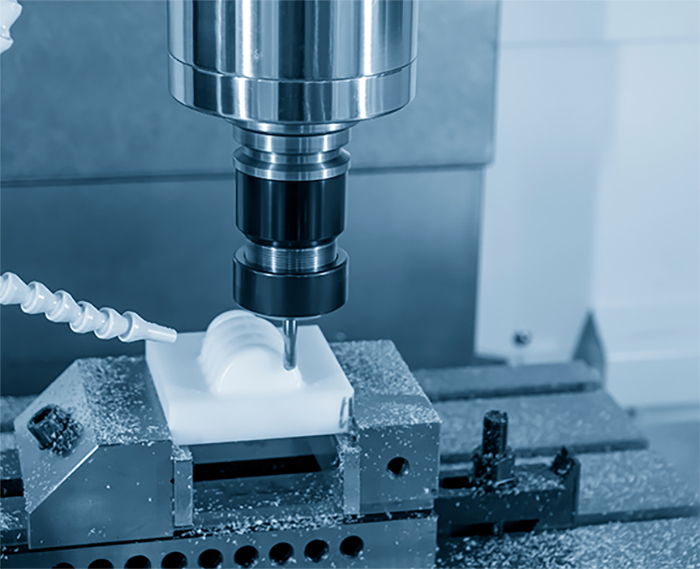
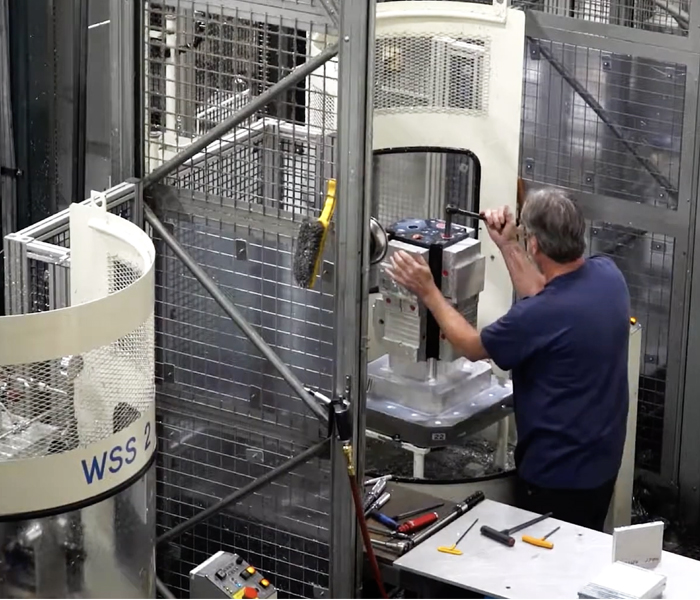
Our advanced turning centers and experienced team excel in producing cylindrical and complex components with exceptional precision and reliability, from prototypes to full-scale production. Equipped with multi-axis capabilities, live tooling, and sub-spindles, our CNC turning centers efficiently machine intricate features while maintaining tight tolerances across a diverse range of part geometries.
The 3-axis CNC mill is the most commonly used type of milling machine, offering full control over the X, Y, and Z axes. Its versatility makes it ideal for handling a broad range of machining tasks.
This type of router enables the machine to rotate along a vertical axis, allowing the workpiece to move for seamless and continuous machining.
5-axis CNC routers feature three traditional axes plus two additional rotary axes, enabling them to machine five sides of a workpiece in a single setup without requiring removal or resetting. The workpiece rotates, while the spindle head moves around it for precise, continuous machining. These machines are larger and more costly but offer unparalleled versatility and efficiency for complex tasks.
- Aluminum 6061: Excellent machinability, corrosion resistance, and good strength-to-weight ratio.
- Aluminum 7075: High strength, excellent fatigue resistance, and lower corrosion resistance compared to 6061.
- Aluminum 2024: Exceptional strength and fatigue resistance, but limited corrosion resistance.
- Aluminum 5052: High corrosion resistance, good formability, and moderate strength.
- Aluminum 5083: Excellent corrosion resistance, especially in marine environments, and high strength.
- Aluminum 6063: Good corrosion resistance, excellent finish, and moderate strength.
- Aluminum MIC-6 (Cast Aluminum Plate): High dimensional stability, excellent flatness, and consistent thickness.
- Aluminum 3003: Good corrosion resistance and excellent workability, but lower strength.
- Brass C360 (Free-Cutting Brass): Excellent machinability, high strength, and corrosion resistance, ideal for precision parts and high-speed machining.
- Brass C353 (High-Leaded Brass): Superior machinability with enhanced wear resistance and good corrosion resistance.
- Brass C464 (Naval Brass): Excellent corrosion resistance, especially in marine environments, with high strength and toughness.
- Brass C272 (Yellow Brass): Good machinability and ductility with moderate corrosion resistance.
- Brass C230 (Red Brass): High corrosion resistance combined with good machinability, notable for its reddish color and durability.
- Brass C385 (Architectural Brass): Offers good machinability and excellent surface finish capability with moderate corrosion resistance.
- Copper C101 (Oxygen-Free Copper): High electrical and thermal conductivity with excellent corrosion resistance and machinability.
- Copper C110 (Electrolytic Tough Pitch Copper): Exceptional electrical and thermal conductivity with good corrosion resistance and moderate machinability.
- Copper C145 (Tellurium Copper): Enhanced machinability due to added tellurium, while retaining high conductivity and corrosion resistance.
- Copper C182 (Chromium Copper): High strength and wear resistance with good conductivity, ideal for high-load applications.
- Copper C122 (Phosphorized Copper): Excellent weldability and corrosion resistance, with moderate machinability.
- Copper C17510 (Beryllium Copper): High strength and hardness with good conductivity and corrosion resistance, suited for high-performance needs.
- Isostatic Graphite: High density and uniformity with excellent thermal and electrical conductivity, ideal for precision applications.
- Extruded Graphite: Lower density and slightly less uniform than isostatic graphite but offers good machinability and thermal shock resistance.
- Vibrated Graphite: Economical with moderate density and uniformity, suitable for less demanding applications.
- High-Density Graphite: Exceptional strength, wear resistance, and high-temperature stability, making it suitable for extreme conditions.
- Ultra-Fine Grain Graphite: Superior surface finish and machinability with excellent thermal conductivity, ideal for detailed and intricate machining.
- Impregnated Graphite:Enhanced strength, wear resistance, and oxidation resistance due to resin or metal impregnation.
- Hastelloy C22: Exceptional corrosion resistance to oxidizing and reducing agents with good weldability and moderate machinability.
- Hastelloy C276: Superior resistance to chemical corrosion, particularly in harsh environments, with excellent formability and weldability.
- Hastelloy C2000: Enhanced versatility with resistance to a wide range of acids and oxidizing agents, offering good strength and moderate machinability.
- Hastelloy X: High-temperature strength and oxidation resistance, combined with good machinability and formability.
- Hastelloy B2: Outstanding resistance to hydrochloric acid and other strongly reducing environments, with moderate machinability.
- Hastelloy G30: Excellent corrosion resistance to phosphoric acids and oxidizing chemicals, with good weldability and moderate machinability.
- Invar 36: Extremely low thermal expansion with excellent dimensional stability and good machinability, making it ideal for precision applications.
- Super Invar: Lower thermal expansion than standard Invar with added strength and stability, suited for extreme precision requirements.
- Invar 42: Moderate thermal expansion with good machinability and high corrosion resistance, commonly used in electronics.
- Invar 32-5: Optimized for low expansion and stability in cryogenic environments with moderate machinability.
- Kovar (Invar Alloy): Low thermal expansion with good machinability and excellent compatibility with glass and ceramics for hermetic sealing applications.
- Pure Molybdenum: High melting point, excellent thermal conductivity, and good machinability for high-temperature applications.
- TZM Alloy (Titanium-Zirconium-Molybdenum): Enhanced strength, creep resistance, and thermal stability with moderate machinability, ideal for demanding environments.
- Lanthanated Molybdenum: Improved ductility and machinability at elevated temperatures, with enhanced resistance to recrystallization.
- Molybdenum-Lanthana (MoLa): High-temperature stability and excellent creep resistance with good machinability for precision components.
- Oxide Dispersion-Strengthened Molybdenum: Superior strength and durability in extreme environments with moderate machinability.
- Copper-Molybdenum (CuMo): High thermal conductivity and strength with improved machinability for thermal management applications.
- Inconel 625: Excellent corrosion and oxidation resistance, high strength, and good weldability with moderate machinability.
- Inconel 718: High strength, creep resistance, and thermal stability, with good machinability when heat-treated.
- Inconel 600: Exceptional oxidation and corrosion resistance at high temperatures, with moderate machinability.
- Inconel 601: Outstanding oxidation resistance and thermal stability, with moderate machinability and good weldability.
- Inconel 725: Superior corrosion resistance and strength, particularly in harsh environments, with moderate machinability.
- Inconel X-750: High-temperature strength and oxidation resistance with good fatigue properties and moderate machinability.
- Inconel 617: Excellent strength and oxidation resistance in high-temperature environments, with good weldability and moderate machinability.
- Stainless Steel 304: Excellent corrosion resistance, good formability, and moderate machinability, widely used in general-purpose applications.
- Stainless Steel 316: Superior corrosion resistance, particularly to chlorides and marine environments, with good machinability and strength.
- Stainless Steel 303: Enhanced machinability due to added sulfur, with good corrosion resistance and moderate strength.
- Stainless Steel 410: High strength and wear resistance with moderate corrosion resistance and machinability.
- Stainless Steel 430: Good corrosion resistance, particularly in mild environments, with moderate machinability and excellent polishability.
- Stainless Steel 17-4 PH: High strength, excellent corrosion resistance, and good machinability after heat treatment.
- Stainless Steel 440C: Exceptional hardness, wear resistance, and moderate corrosion resistance with lower machinability.
- Stainless Steel 321: Excellent resistance to high-temperature oxidation and intergranular corrosion, with good machinability.
- Stainless Steel 2205 (Duplex): High strength, excellent corrosion resistance, and moderate machinability, particularly suited for harsh environments.
- Titanium Grade 1: Excellent corrosion resistance, high ductility, and good machinability, ideal for applications requiring formability.
- Titanium Grade 2: Strong corrosion resistance with moderate strength and good machinability, commonly used in industrial and marine environments.
- Titanium Grade 5 (Ti-6Al-4V): High strength-to-weight ratio, excellent corrosion resistance, and moderate machinability, widely used in aerospace and medical applications.
- Titanium Grade 9 (Ti-3Al-2.5V): Good corrosion resistance, moderate strength, and better cold-forming capabilities than Grade 5, with fair machinability.
- Titanium Grade 23 (Ti-6Al-4V ELI): Enhanced biocompatibility, excellent strength, and corrosion resistance with moderate machinability, used in medical implants.
- Titanium Grade 12: High corrosion resistance to acidic and oxidizing environments, moderate strength, and fair machinability.
- Beta Titanium Alloys: Superior formability and strength with moderate corrosion resistance, offering challenging but feasible machinability.
- Pure Tungsten: Extremely high density, excellent thermal and electrical conductivity, and high melting point, with challenging machinability due to its hardness.
- Tungsten Heavy Alloy (WHA): High density and strength with improved machinability compared to pure tungsten, suitable for precision components.
- Tungsten Carbide: Exceptional hardness, wear resistance, and high-temperature performance, with limited machinability requiring specialized tools.
- Tungsten-Copper Alloy: Good thermal and electrical conductivity with moderate machinability, commonly used in thermal management applications.
- Tungsten-Rhenium Alloy: Enhanced ductility and strength at high temperatures, with challenging but manageable machinability.
- Tungsten-Molybdenum Alloy: Improved machinability and thermal resistance, combining the benefits of both materials for high-temperature environments.
We provide a wide range of post-processing services, both in-house and through trusted partners, to enhance the performance, durability, and appearance of manufactured parts.
Protective and decorative coating for metals, including titanium, teflon-based finishes, and hard chrome using sulfuric acid.
Heat treatments to improve material properties like hardness and durability.
Abrasive cleaning method for surface preparation or achieving a matte finish.
Surface conversion for steel and other metals, providing corrosion resistance and a sleek, black finish.
Provides corrosion resistance and prepares surfaces for paint adhesion.
Thin, lubricative coatings that reduce friction and wear on parts.
Processes to enhance material strength, durability, and performance.
Application of protective coatings to reduce friction and enhance performance.
Protects specific areas during finishing processes or creates unique visual effects.
Ensures part integrity without causing damage, ideal for quality assurance.
Use of nitric or citric acid to remove contaminants and enhance corrosion resistance on stainless steel.
Dye-based method to detect surface defects in materials.
Removes impurities and prepares surfaces for finishing or storage.
Metal coatings such as zinc, chromium, nickel, copper, and gold to improve wear resistance, corrosion protection, and conductivity.
Creates a smooth, high-gloss finish while improving corrosion resistance.
Durable, high-quality finishes applied electrostatically and cured for enhanced surface protection.
Adds protective coatings or aesthetic finishes for various applications.
Strengthening process that improves fatigue life and resistance to cracking by introducing residual compressive stress.
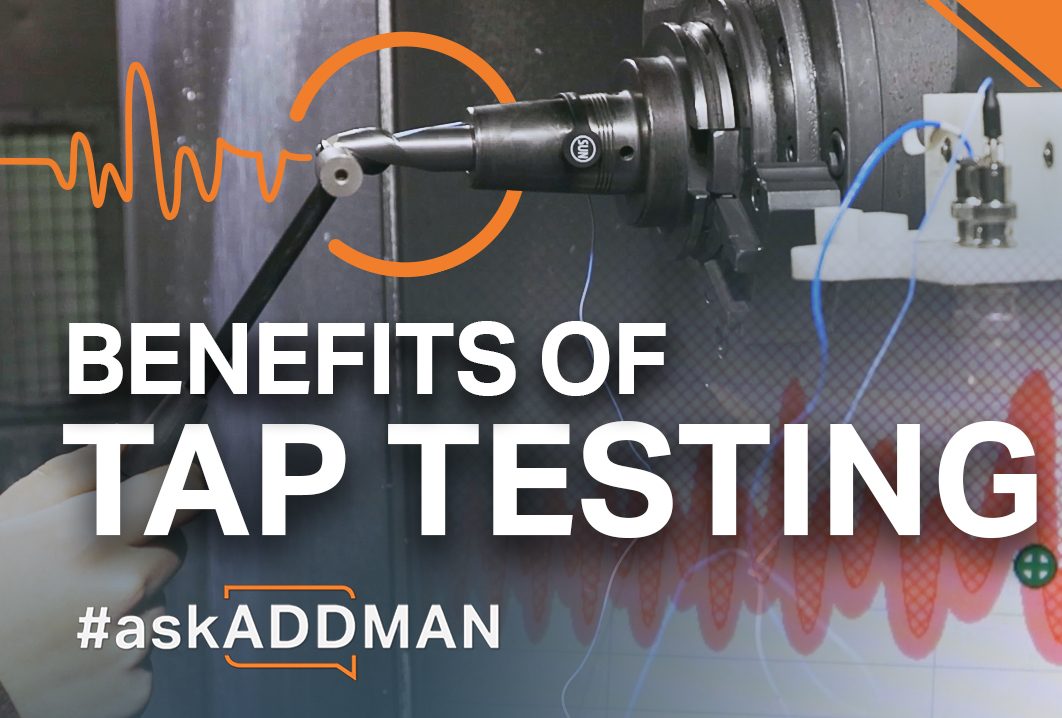