CF3D® technology combines additive manufacturing, robotics, and advanced composite materials to address the critical demands of the aerospace and defense industries.
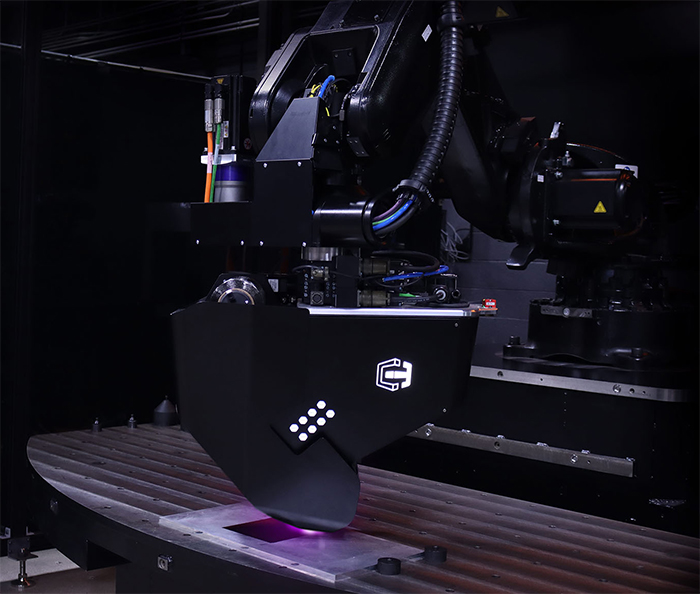
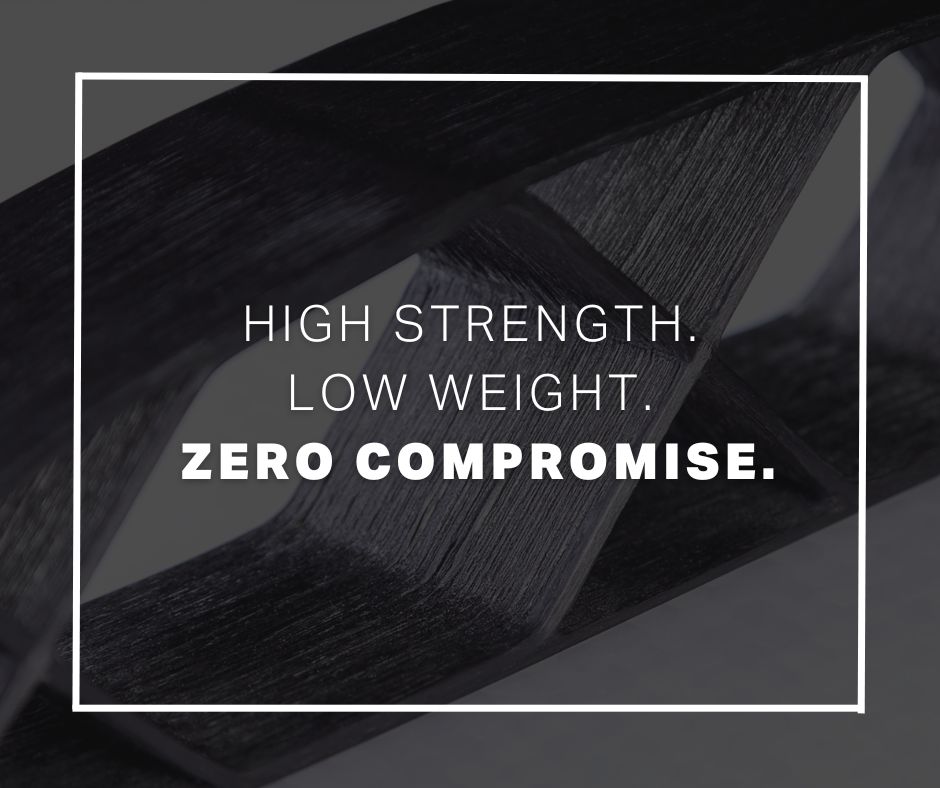
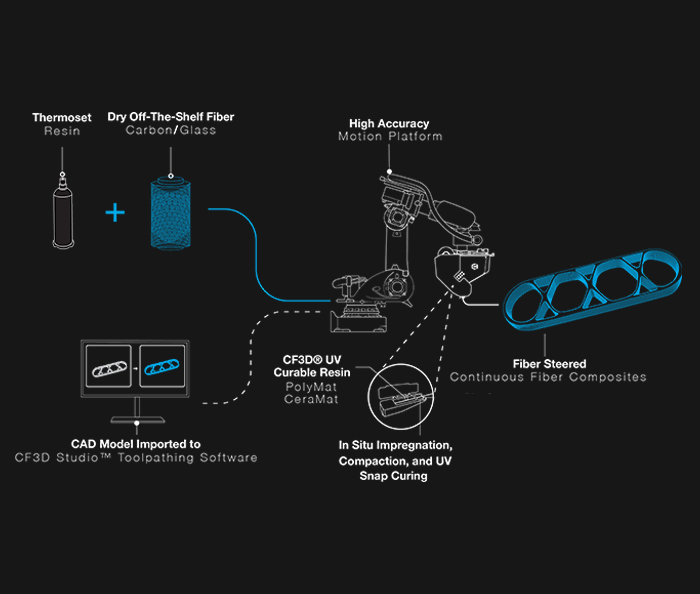
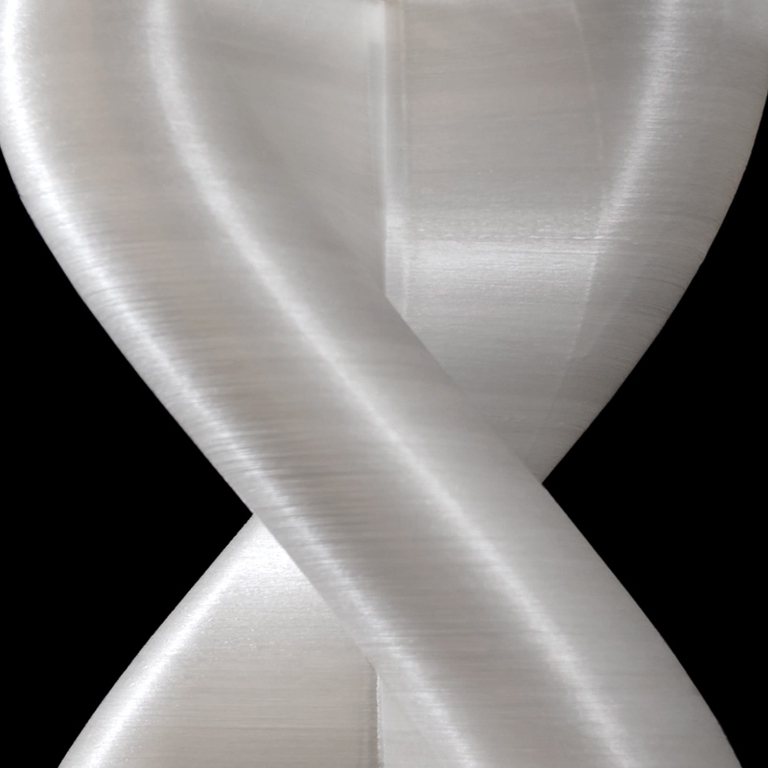
Customer Benefits
Lightweight Solutions with High Strength
Our composite parts combine the best of both worlds: lightweight construction with high strength, making them ideal for applications where reducing weight is crucial without sacrificing durability.
Customizable Strength and Durability
With control over fiber orientation, we tailor each part to meet specific strength and durability needs. This customization leads to parts optimized for individual applications, enhancing both performance and longevity.
Cost-Effective Alternative to Metal
Composite printing provides a cost-effective solution where weight reduction and strength are required but full metal parts aren’t necessary. Customers benefit from similar structural integrity at a fraction of the cost.
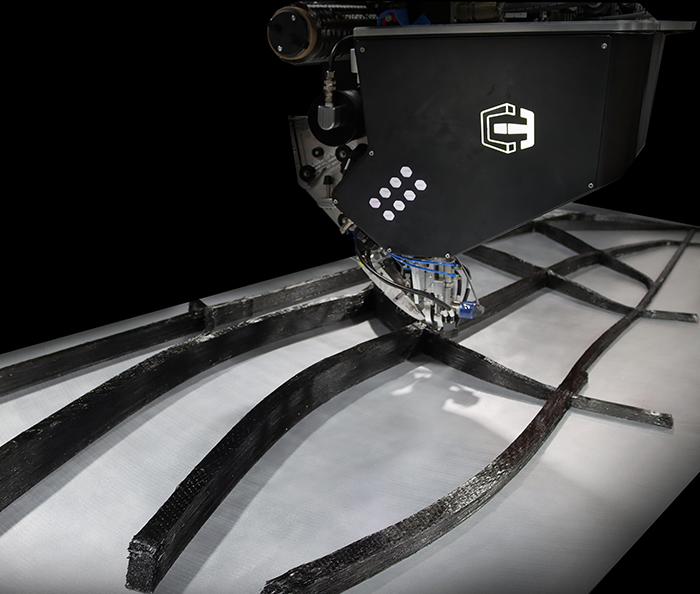