Selective Laser Sintering (SLS) is an advanced 3D printing technology that utilizes a CO₂ laser to selectively melt cross-sections of powdered thermoplastic material, building up a 3D structure layer by layer.
SLS
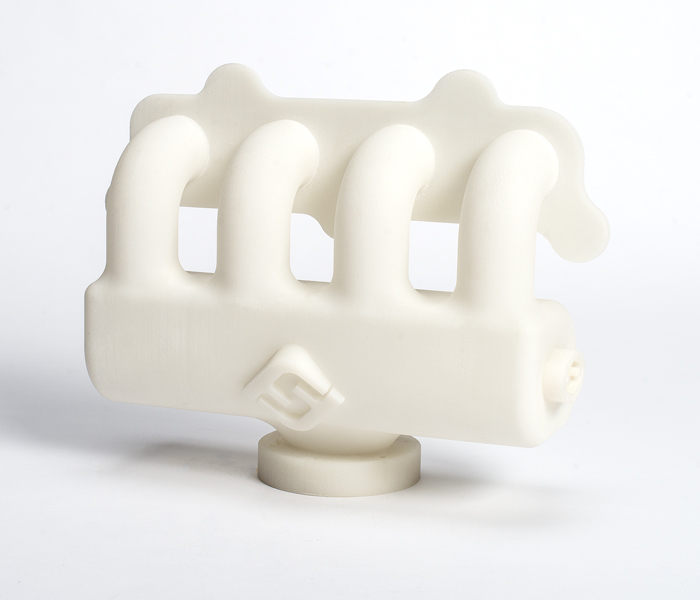
Precision and Durability
SLS technology is unique in that parts are built within a powder bed, eliminating the need for support structures. This allows designers and engineers to incorporate complex internal features such as ducts, undercuts, and intricate geometries without the risk of damaging the part during the removal of supports. This also reduces post-processing time and effort, making the process more efficient.
Key Benefits:
- Support-Free Design: The powder bed eliminates the need for supports, enabling more complex designs and reducing post-processing.
- Material Flexibility: SLS can produce parts that are durable, tough, flexible, or lightweight, depending on material selection and design requirements.
- Durable and Lightweight Parts: Parts created using SLS are ideal for functional prototypes and end-use applications where strength, toughness, and lightweight properties are needed.
- Versatile Material Options: From impact-resistant engineering plastics to flame- or chemical-resistant materials, SLS can produce parts capable of withstanding harsh and demanding environments.
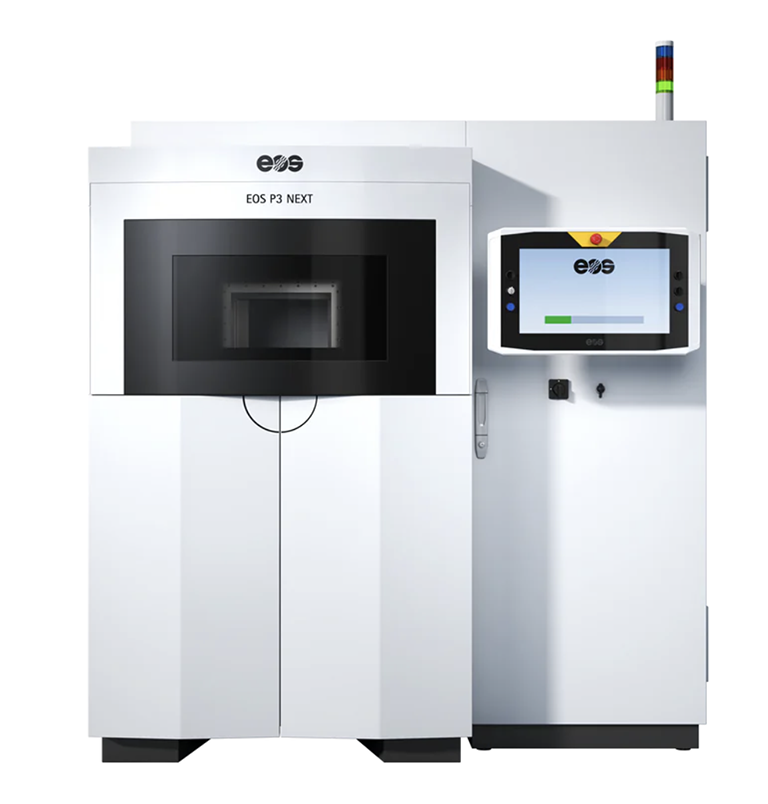
EOS P3 NEXT - Redefining SLS Technology
The EOS P3 NEXT is a cutting-edge Selective Laser Sintering (SLS) 3D printer designed to revolutionize polymer manufacturing with its unparalleled combination of precision, efficiency, and versatility. Ideal for industrial-scale production, including advanced medical applications, this machine embodies the next generation of additive manufacturing technology.
Technical Specifications:
- Build Volume: 340 x 340 x 600 mm (13.4 x 13.4 x 23.6 in)
- Laser Type: CO₂; 1 x 70 W
- Scan Speed: Up to 6.0 m/s (19.7 ft/s)
- Focus Diameter: Approx. 480 µm (0.01890 in)
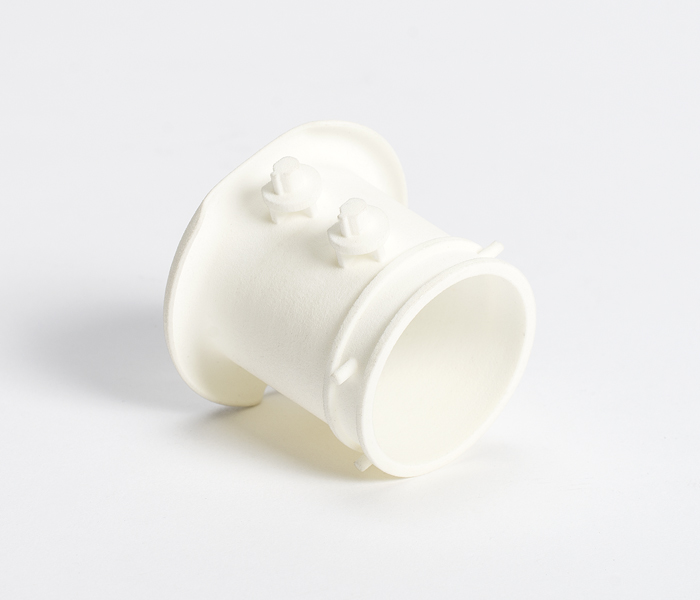
Applications
Selective Laser Sintering technology, also called SLS, builds with a CO₂ laser that selectively melts cross-sections of a design in powdered thermoplastic material, creating a 3D structure. Nylon is the most popular base material for SLS, and it can be combined with plastic, ceramic, glass, metal, or other materials for more robust parts.
- Complex geometries
- Lightweight Parts
- Rapid prototyping
- Both Small & Large Build Volumes
- High-heat applications
- Chemically, heat, UV light, water resistant parts
- Excellent Mechanical characteristics