Haynes 282 is a nickel-based superalloy specifically engineered for high-temperature applications that demand exceptional strength, stability, and resistance to thermal fatigue.
Haynes 282
High-Performance Alloy for Extreme Temperatures
Haynes 282 is a nickel-based superalloy specifically engineered for high-temperature applications that demand exceptional strength, stability, and resistance to thermal fatigue. Developed to fill the gap between older alloys like Waspaloy and modern superalloys, Haynes 282 offers a unique combination of excellent creep strength, thermal stability, and weldability. This makes it an ideal choice for critical applications in the aerospace, power generation, and industrial gas turbine sectors, where reliable performance under extreme conditions is paramount.
Key Properties
- Exceptional Creep Strength: Haynes 282 exhibits outstanding creep strength at temperatures up to 1800°F (982°C), making it highly suitable for components subjected to prolonged stress at elevated temperatures.
- Thermal Stability: The alloy maintains its mechanical properties and resists microstructural changes over long-term exposure to high temperatures, ensuring durability and reliability in demanding environments.
- Superior Weldability: Unlike many high-temperature alloys, Haynes 282 offers excellent weldability without compromising its mechanical properties, making it easier to fabricate complex structures.
- Oxidation and Corrosion Resistance: Haynes 282 provides excellent resistance to oxidation and corrosion at high temperatures, which extends the life of components in harsh environments.
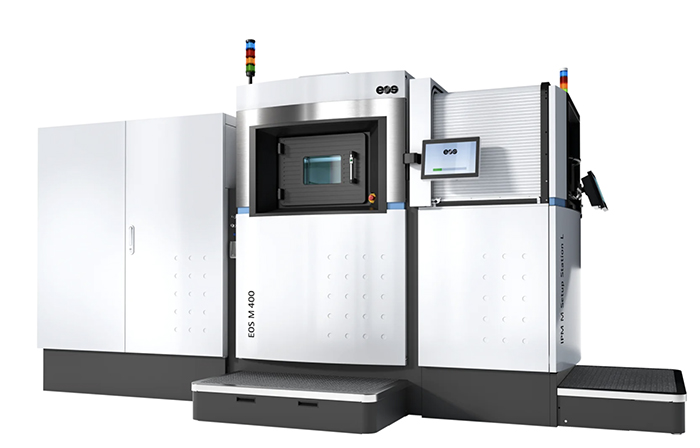
EOS M400-1
ADDMAN utilizes the EOS M400-1 to produce Haynes 282 parts with exceptional precision and efficiency. This advanced machine features a substantial build volume and a powerful laser, enabling the creation of complex Haynes 282 components with outstanding accuracy and consistent quality. The M400-1’s cutting-edge capabilities and material versatility make it the ideal choice for delivering high-performance Haynes 282 parts across a wide range of demanding industrial applications.
Aluminum AlSi10Mg is available in various forms, including powders for additive manufacturing, which allows for the production of complex geometries and lightweight structures. It is also well-suited for traditional manufacturing methods such as casting and machining. The alloy’s excellent castability and machinability make it highly versatile for a wide range of industrial applications.
- Automotive: AlSi10Mg is used in the production of lightweight components such as engine parts, transmission housings, and structural elements that require a balance of strength and weight.
- Aerospace: The alloy is employed in aerospace applications for parts that need to withstand high stress while maintaining low weight, such as brackets, housings, and structural components.
- Consumer Electronics: Due to its thermal conductivity and lightweight nature, AlSi10Mg is ideal for electronic housings, heat sinks, and other components that require efficient heat management.
- Tooling: AlSi10Mg is also used in the production of molds and tooling, where its durability and resistance to thermal fatigue ensure long service life.