Inconel 718 is the go-to superalloy for industries demanding top-tier strength, corrosion resistance, and high-temperature performance. Whether you’re optimizing components for aerospace, energy, or chemical processing, Inconel 718 delivers unmatched reliability in the most challenging conditions.
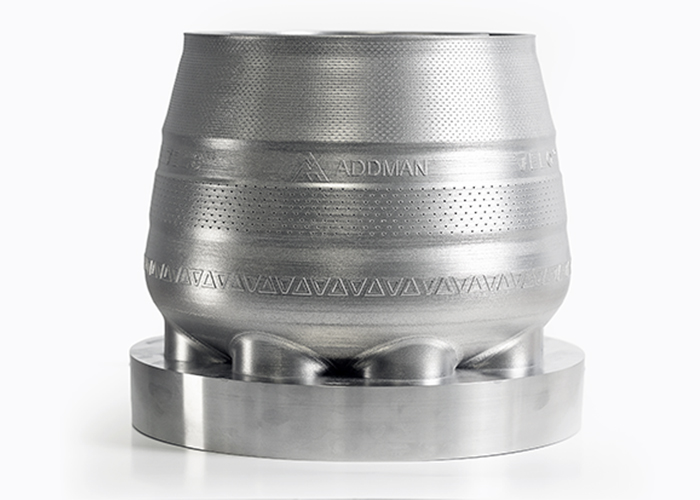
TENSILE STRENGTH | YIELD STRENGTH | ELONGATION | |||
---|---|---|---|---|---|
As Printed | With Heat Treatment | As Printed | With Heat Treatment | As Printed | With Heat Treatment |
140 ksi | 140 ksi | 88 ksi | 88 ksi | 30% | 17% |
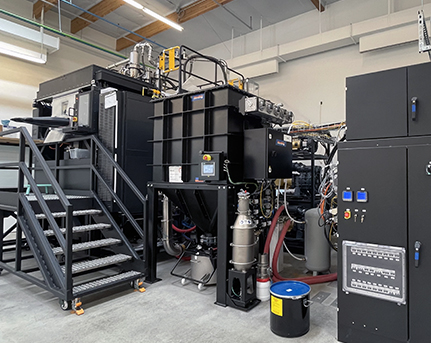
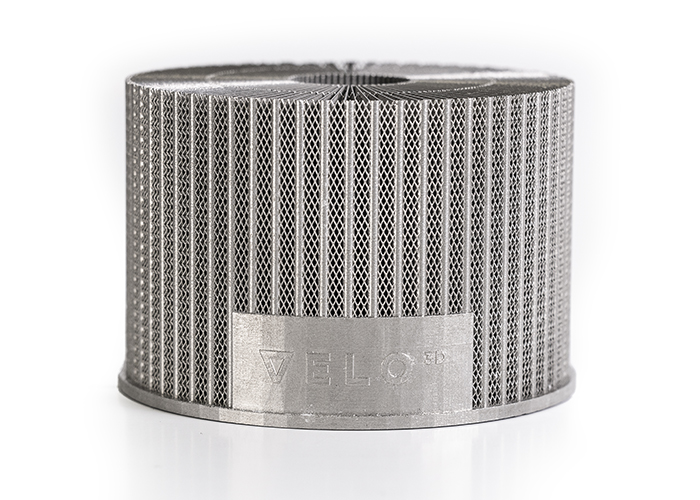