Based in Rochester, MO, ADDMAN Precision, formally known as Domaille Engineering, excels in producing cold plates and manifolds from exotic materials.
To conveniently access our Terms and Conditions as well as Purchasing and Quality Clauses, all you need to do is click on the collapsible menus provided below.
- DEFINITIONS. As used in these Terms and Conditions of Purchase (“Terms and Conditions”), Domaille Engineering, LLC. shall be referred to as “Domaille Engineering,” the company supplying goods or services under this purchase order (the “Purchase Order”) shall be referred to as “Supplier,” and the term “goods” means the goods, pieces, merchandise, materials, equipment, supplies, and products or services ordered.
- OFFER TO PURCHASE. This Purchase Order, provided that it is not a blanket order that provides merely an estimate of amounts to be purchased within a defined time period, is an offer to purchase the goods. To the extent this Purchase Order is in any way deemed to be an acceptance of a quotation or other offer by Supplier, any such acceptance is expressly conditioned upon the consent of Supplier to the Terms and Conditions.
- ACCEPTANCE. Any of the following acts by Supplier shall constitute acceptance of this Purchase Order: signing and returning a copy of this Purchase Order; commencement of performance or informing Domaille Engineering in any manner of commencement of performance; or returning Supplier’s form of acknowledgment. Acceptance of this Purchase Order constitutes agreement by Supplier to these Terms and Conditions and agreement by Supplier to deliver as specified under the Terms and Conditions. Notwithstanding provisions of section 2-207 of the Minnesota UCC, no term or condition included in any writing of acceptance by Supplier shall be deemed to be part of the agreement between the parties unless Supplier has requested and received written assent thereto by an authorized representative of Domaille Engineering. Any acceptance of this Purchase Order is limited to acceptance of the express terms of the offer contained herein.
- VARIATION OR MODIFICATION. Additional or different terms, or any attempt by Supplier to vary in any degree any of the terms of this Purchase Order, shall be deemed material and shall be rejected. No variations or modifications in the provisions of this Purchase Order including, without limitation, the description, quantity, price or delivery schedule will be effective against Domaille Engineering unless agreed to in writing and signed by Domaille Engineering’s authorized representative.
- INTENTIONALLY LEFT BLANK
- DELIVERY. The delivery and performance requirements and specified dates of this Purchase Order shall be strictly adhered to and shall not be changed or modified without Domaille Engineering’s prior written consent. In the event of failure to deliver or perform by the dates specified in a Purchase Order, Domaille Engineering reserves the right to cancel such Purchase Order in total or any unexecuted part of such Purchase Order. If no delivery date is shown, delivery shall be made within a reasonable time. Domaille Engineering’s count shall be accepted as conclusive on all shipments not accompanied by a packing slip.
- PACKAGING. Goods shall be packed to meet carrier requirements and to ensure the lowest transportation rates consistent with adequate protection. Any extra expenses affecting delivery of goods not so shipped will be charged to Supplier. Domaille Engineering shall not be liable for any packaging charges, unless otherwise agreed to in advance in writing. All goods, wrappers, and containers must bear markings and labels required by applicable federal, state, and municipal laws and regulations.
- SHIPPING DOCUMENTS AND CONTAINERS. The shipping destination for goods must appear on all shipping containers and on all documents, invoices, and correspondence. Supplier shall forward to Domaille Engineering with the invoice the express receipt or bill of lading signed by the carrier, evidencing the fact that shipment has been made. All expenses incurred by Supplier’s failure to furnish necessary shipping documents shall be charged to Supplier.
- FOB; DAMAGE DURING DELIVERY. Delivery of goods under this Purchase Order shall be by FOB: Domaille Engineering, Rochester, Minnesota, and unless other agreed and/or stated in this Purchase Order, the risk of loss or damage shall remain with the Supplier until actual delivery to Domaille Engineering. Supplier shall be responsible for damages sustained during delivery. Any resulting claims against carriers shall be the responsibility of the Supplier. Replacement of any damaged goods shall be the sole responsibility of Supplier.
- PAYMENT AND TERMS. Unless otherwise stated in this Purchase Order, terms of payment shall be 30 days net, or as negotiated by Domaille Engineering and Supplier. Payment and cash discount periods shall start with the date of receipt of proper invoice or date of delivery, whichever is later. Domaille Engineering shall not, by making prompt payment or payment prior to inspection, be deemed to have accepted any goods or to have waived any claim for adjustment or any other claim against Supplier.
- INSPECTION. Goods shall be subject to inspection, test, and count by Domaille Engineering after receipt at destination. If any goods shall be defective in material or workmanship or otherwise not in conformity with the requirements of this Purchase Order, Domaille Engineering, in addition to its other rights, may reject same for full credit or require prompt correction or replacement at Supplier’s expense, including replacement costs for any raw material or semi-finished products or components supplied, labor and transportation. Goods which are defective or of an unauthorized quantity or not in accordance with specifications will be held for 30 days from and after date of discovery of defect by Domaille Engineering for Supplier’s instruction at Supplier’s risk; and if Supplier so directs or if no instructions are sent within 30 days, goods will be returned at Supplier’s expense. If inspection discloses that part of the goods received is not in accordance with Domaille Engineering’s specifications, Domaille Engineering shall have the right to cancel any unshipped portion of its order.
- QUANTITY. Shipments must equal exact amounts ordered unless otherwise agreed to by Domaille Engineering.
- TIME IS OF THE ESSENCE. Time of delivery and of all other aspects of performance hereunder is of the essence of this Purchase Order. If any goods are not received, or any element of service not performed by the date specified, Domaille Engineering may, at its option and without notice to Supplier, either approve a revised date or cancel all or a portion of the Purchase Order or obtain the goods elsewhere.
- CHANGES BY DOMAILLE ENGINEERING. Domaille Engineering shall have the right, by giving notice to Supplier, to make changes in the drawings, designs, and specifications for the goods, or the method of shipment or packing or the place of inspection, delivery, or acceptance. Upon receipt of any such notice, Supplier shall proceed promptly to make such changes in accordance with the terms of such notice. Supplier shall deliver to Domaille Engineering, within 15 days, a statement showing the effect of any such change in the cost of, or the time required for performance of this Purchase Order, and an equitable adjustment shall be made in the price or delivery schedule or both.
- CANCELLATION AND RESCHEDULING. Domaille Engineering may cancel this Purchase Order in whole or in part without charge prior to shipment of the goods or commencement of performance of the services by written notice to Supplier. Equitable payments/adjustments may be made for work performed prior to cancellation. Domaille Engineering may reschedule the time and place of delivery of goods under this Purchase Order in whole or in part without charge prior to shipment of the goods or commencement of services by written notice to Supplier. Cancellation or rescheduling under this Section shall not be deemed to be a breach of contract.
- DISCREPANCIES. In case of any discrepancies or questions, Supplier shall refer to Domaille Engineering for decision, instruction, or interpretation.
- CONFIDENTIAL INFORMATION. All drawings, data, designs, specifications, tools, materials, and other property furnished by Domaille Engineering shall be confidential, shall remain Domaille Engineering’s property, shall be used by Supplier only in the performance of this Purchase Order, and together with all copies thereof, shall be redelivered to Domaille Engineering or destroyed by Supplier as Domaille Engineering specifies. Supplier assumes all risks of loss or damage to any such drawings, specifications, tools, materials, or other property, and shall redeliver the same to Domaille Engineering (when specified by Domaille Engineering) in the same condition as when received by Supplier except for reasonable wear and tear of utilization in the performance of this Purchase Order. This Purchase Order is confidential between Domaille Engineering and Supplier, and it is agreed by Supplier that none of the details connected herewith shall be published or disclosed to any third party without Domaille Engineering’s written permission.
- WARRANTIES. Supplier expressly warrants that all goods will conform to any applicable specifications, drawings, samples, or other descriptions and will be merchantable, of good workmanship and material, fit for the purpose for which intended, and free from defect. Such warranties shall survive inspection, test, acceptance, and payment. Acceptance of this Purchase Order shall constitute an agreement upon Supplier’s part to indemnify and hold Domaille Engineering harmless from all liability, loss, damage, and expense including reasonable attorneys’ fees incurred or sustained by Domaille Engineering by reason of the failure of the goods to conform to such warranties. Such indemnity shall be in addition to any other remedies provided by law.
- INDEMNIFICATION.
19.1 If any work or services are to be performed on any premise of Domaille Engineering pursuant to this Purchase Order, Supplier shall indemnify Domaille Engineering and hold Domaille Engineering harmless against and from any and all losses, liabilities, and claims, including costs and expenses for property loss or damage or bodily injury or death resulting directly or indirectly from the performance of such work or services. Supplier shall give Domaille Engineering a policy or certificate of public liability insurance, with such insurance carrier and with such limits as Domaille Engineering may reasonably require, insuring Domaille Engineering, primary to any other insurance available to Domaille Engineering, against any and all such losses, liabilities, and claims.19.2 If Supplier is furnishing any goods, or products which become a part of any goods or product of Domaille Engineering or others, then Supplier will further indemnify and save harmless Domaille Engineering, its employees, agents, and representatives from and against any and all demands of every nature and kind including without limitation reasonable attorneys’ fees and disbursements incurred in defense of any claim or demand arising out of injury to or death of or property damage to any third person if said injury, death, and/or property damage is in any way caused from any act or omission on the part of Supplier, its agents, employees, or subcontractors except to the extent that any loss or damage is due solely and directly to the gross negligence of Domaille Engineering. This indemnification includes but is in no way limited to any defect in goods, materials, products, or services in either manufacture or design.19.3 Supplier agrees to indemnify and hold Domaille Engineering harmless against any and all losses, liabilities, and claims that may be brought or assessed by any party whatsoever against Domaille Engineering as a result of Supplier’s failure to complete its performance of this Purchase Order in full on or before the delivery date set forth in this Purchasing Order.
- INTELLECTUAL PROPERTY INFRINGEMENT. With respect to the goods provided under this Purchase Order, Supplier shall defend, indemnify and hold harmless Domaille Engineering, its directors, officers, employees, agents, and affiliates for and against any and all liabilities, claims, damages, expenses, and costs (including reasonable legal fees and expenses) arising from or related in any way to a violation or infringement of any patent, copyright, trademark, trade dress, and trade secret, or any other contractual right, proprietary right or intellectual property right, of any third party.
- DEFAULT. Domaille Engineering may, by written notice to the Supplier, terminate the whole or any part of this Purchase Order if (i) Supplier fails to make delivery of any goods within the time specified, or (ii) Supplier delivers any goods that do not conform to contractual requirements, or (iii) Supplier fails to perform any other provision of this Purchase Order, or (iv) so fails to make progress as to endanger performance of this Purchase Order in accordance with its terms, or (v) Supplier becomes insolvent or subject to proceedings under any law relating to bankruptcy or the relief of debtors. Domaille Engineering may, in addition to its other rights, procure upon such terms and in such manner as Domaille Engineering may deem appropriate substitute goods or services similar to the goods so terminated; and Supplier shall be liable to Domaille Engineering for any excess costs of such similar goods or services, except that Supplier shall not be liable for such excess costs if Supplier’s default is due to a cause beyond its control and without its fault or negligence including Acts of God, force majeure, war, flood, fire, act of any government, or catastrophe. Acceptance of any part of the goods covered by this Purchase Order does not bind Domaille Engineering to accept future shipments nor deprive it of the right to return goods already accepted.
- SET-OFFS. All claims for money due or to become due from Domaille Engineering shall be subject to deductions by Domaille Engineering for any set-off or counterclaim arising out of this or any other of Domaille Engineering’s purchase orders or agreements with Supplier, whether such set-off or counterclaim arose before or after any assignment by Supplier.
- TAXES. The prices for the goods include all federal, state, and local taxes imposed on the goods or the sale thereof; but no such tax shall be included for which an exemption is available. Supplier shall separately state on each invoice the amount of any such tax and shall indemnify Domaille Engineering against liability for any tax not so stated. In the event that it shall be determined that any tax included in any price was not required to be paid, Supplier will notify Domaille Engineering, will make prompt application for the refund thereof, and will make prompt payment to Domaille Engineering of the amount of any refund.
- ASSIGNMENT. No obligation under this Purchase Order shall be delegated or assigned by Supplier without the prior written consent of Domaille Engineering, and any purported subcontracting, delegation, or assignment without such consent shall be void.
- ENTIRE AGREEMENT. This Purchase Order, including the Terms and Conditions, and any document referred to herein constitute the entire contract between the parties relating to the subject matter hereof and supersede all prior understandings, transactions, communications, or writings in respect of such subject matter. It may not be modified or terminated orally; and no claimed modification, termination, or waiver shall be binding unless in writing and signed by the party against whom such claimed change, termination, or waiver is sought to be enforced.
- GOVERNING LAW, VENUE, WAIVER OF JURY TRIAL. Any Domaille Engineering Purchase Order and these Terms and Conditions shall be governed by the laws of the State of Minnesota, excluding its choice of law rules. DOMAILLE ENGINEERING AND SUPPLIER EACH WAIVES ALL RIGHTS TO TRIAL BY JURY IN CONNECTION WITH ANY DISPUTE THAT ARISES OUT OF OR RELATES IN ANY WAY TO THIS PURCHASE ORDER.
- COUNTERFEIT PRODUCT. Supplier shall only produce products or purchase components/hardware direct from the original component manufacturer (i.e., OCM), original equipment manufacturer (i.e., OEM), through an authorized distributor (i.e., Franchised) or a Buyer’s authorized source. Work shall not be acquired from independent distributors or brokers without written approval from Buyer. The Buyer must be notified immediately if the Supplier suspects they may have supplied counterfeit products. Work that is delivered that contains or includes counterfeit products will be replaced at the Supplier’s expense, with certified genuine products.
- ETHICAL BEHAVIOR. To supply top-quality products and services responsibly, we understand and expect that our suppliers will have an internal code of ethics and business conduct, and will maintain compliance with all laws and regulations applicable to your operation of business.
- SPECIAL PROCESSES. Suppliers providing special processing must maintain a system for validating processes similar to that of a NADCAP program, or other system as required by purchase order.
Revisions
Rev. | Author | Date | Summary of change |
A | MLZ | 6/5/2017 | Initial release |
B | MLZ | 7/26/2017 | Added terms for counterfeit parts, ethical behavior, special process controls |
C | JSR | 11/13/2020 | Update formatting |
P01 – PRECISION PARTS
These are precision parts produced at substantial cost. They must be handled with care and repackaged in the original shipping container. No nicks, dents, or abrasions will be tolerated.
P02 – MSDS SHEET
Please send a “Material Safety Data Sheet” that meets the OSHA hazard communication standard on all potentially hazardous chemicals or materials with your shipment.
P03 – BUYER RETAINS TITLE
Buyer retains title to all drawings, designs, specifications, and technical data furnished to Supplier for use with this order. All documents are to be treated as Buyer’s confidential information, which shall be used by Supplier only to complete this order and shall be returned upon completion or termination of this order along with all copies or reproductions of the documents. All materials, including tools, special dies and patterns, or anything specifically paid for by the Buyer, shall be the property of the Buyer; shall be returned to the Buyer when no longer required; shall be segregated and clearly identified as property of the Buyer; and shall be used only to produce parts exclusively for the Buyer. Supplier assumes all risk and liability for loss or damage, except for normal wear and agrees to permit inspection and to supply detailed statement of inventory upon request from Buyer.
P04 – INSURANCE CLAUSE
Supplier is to maintain all necessary liability insurance to protect themselves against claims for bodily injury or death of any person or persons whether or not employed by contract, which may arise from any operation in connection with work covered by this order. Required insurance in all cases will be Workman’s Compensation and Employer’s Liability for the state involved, and Public Liability Insurance. If you select any portion of this order, it will be necessary that you carry Supplier’s Protective Liability Insurance. A copy of your “Certificate of Liability Insurance” must be forwarded to Buyer prior to beginning work on this order. You must provide a safe work environment. Supplier will abide by Buyer’s safety policy of wearing safety glasses with side shields at all times in designated areas.
P05 – DROP SHIPMENTS
Please Note: This is a drop shipment to another company. On the same day the shipment is made, a copy of either the packing slip or a shipping document must be sent to the attention of the Buyer on the purchase order.
P06 – SEND ACKNOWLEDGEMENT
Send acknowledgement of purchase order with price and delivery within 48 hours.
P07 – TRACEABILITY AND IDENTIFICATION
Material requiring heat lot traceability will be individually identified and traceable to the purchase order.
P08 – UNIQUE IDENTIFICATION
All items shall be identified with the specific identification requirements per purchase order and drawings.
P09 – DOMESTIC MATERIAL RECEIVED
Preference for certain domestic commodities – DFARS 252.225.7009.
P10 – BUY AMERICAN ACT
Buy American Act – DFAR 252.225-7001
P11 – PHYSICAL MATERIAL ID
Physical Material Identification: Supplier is required to identify each piece of physical material being shipped with information from the purchase order. The information required is: (a) the part number; (b) the part number revision level; (c) the heat lot number, where applicable.
P12 – BAN TEXT MESSAGING WHILE DRIVING
Encouraging Supplier Policies to Ban Text Messaging While Driving – FAR 52.223-18 Contract value exceeds $3,000
P13 – EMPLOYMENT REPORTS ON VETERANS
Employment Reports on Veteran – FAR 52.222-37 Contract value exceeds $100,000
P14 – INTEGRITY OF UNIT PRICES
Integrity of Unit Prices – FAR 52.215-14 Contract value exceeds $150,000
P15 – CONFLICT MATERIALS
Reporting of 3 T and G usage (i.e., Tin, Tantalum, Tungsten and Gold)
P16 – ITAR
This purchase order may contain and/or reference documents containing information subject to the International Traffic in Arms Regulations (ITAR). Suppliers may not export, release, or disclose such information to foreign nationals without first complying with export license requirements of ITAR.
P17 – ROHS/REACH
• the REACH SVHC list dated January 19, 2021
• the EU RoHS 10 Substances Amendment Directive
• the EU Waste Framework Directive (WFD) if REACH SVHCs have been declared
Information can be found at the following link: https://echa.europa.eu/candidate-list-table
Q01 – CERTIFICATE OF CONFORMANCE
Seller is required to submit with each shipment a Certificate of Conformance (C of C) signed or stamped by a Quality Representative or relevant authority. The C of C shall reference the Buyer’s Purchase Order Number, Part Number, Part Revision, Quantity of Parts Processed, and Serial Number (if applicable). The C of C must also state that the materials furnished to the Buyer are in conformance with all requirements listed on the purchase order, drawings, applicable regulatory and/or statutory requirements, and standards with their specified revision level. Supporting documentation will be on file, including approved written procedures for all special processes.
Q02 – TEST CERTS
A copy of the actual test report(s) referencing Buyer’s purchase order, supplier name and address, and/or independent laboratory’s name and address, part number(s), part name, serial number if applicable, lot/batch, list of parameters tested, and test date, must accompany each shipment. These reports shall be verified by an authorized quality representative or relevant authority of Supplier’s company by signature or inspection stamp.
Q03 – MATERIAL CERTS
A copy of the actual chemical composition and actual mechanical properties for each lot, batch, or heat, shall accompany each shipment and must reference Buyer’s purchase order number. Buyer’s purchase order number shall be referenced on the cert, or the packing list shall reference the Buyer’s purchase order number and mill cert.
Q04 – TEST SAMPLES
Test sample(s) shall be submitted with each shipment to conduct tests in accordance with the purchase order requirements and/or referenced specification. Each sample shall be clearly marked to provide traceability to shipped materials.
Q05 – SOURCE INSPECTION
Source inspection is required prior to shipment from your facility. Notify Buyer’s Quality Assurance Department when articles are ready for inspection at: domaillequality@domaillecompanies.com or 507-281-0275
Q06 – PROCESS APPROVAL
Your process(s) must be approved by our customer before performing any specialized processing to this purchase order. You are required to notify Buyer’s Quality Assurance of any changes which may negate any previous qualifications, certifications, and approval statuses, as related to this material.
Q07 – CONTROL CHANGES
The Supplier is responsible for controlling changes to product manufactured or processed to drawings, specification and or purchase order requirements. The Supplier shall notify Buyer and obtain approval prior to any proposed changes to approved designs, processes, fabrication methods, or non-conforming materials prior to incorporating the change and delivery of the product.
Q08 – CRITICAL PARTS
Articles covered by this order have been identified as critical. Supplier is required to assure that affected employees are aware of the critical nature of these articles and that appropriate steps are taken to safeguard product quality.
Q09 – PACKAGING
Supplier shall provide all necessary care in packaging to ensure Buyer’s parts or materials are not damaged. Stacking of plates, bars, sheets, coils, castings, or parts, shall not cause warping, distortion, nicks, dents, gouges, scratches or other damage, inadequate use of pallets, cardboard, bags, boxes, containers, bubble wrap. Styrofoam chips, foam, paper media, etc. meant to protect parts or material delivered to Buyer or to another destination on Buyer’s behalf, shall not be the cause of material or part damage.
Q10 – GOVERNMENT INSPECTION
During performance on this order, Supplier’s quality control or inspection system and manufacturing processes are subject to review, verification, and analysis by authorized Government representatives. Government inspection or release of product prior to shipment is not required unless otherwise notified.
Q11 – DO DEFENSE RATED
This is a DO Defense Rated order. The material is needed at the “ship to” location on the specified “delivery required” date. Supplier is required to give this order priority over unrated orders and orders with lower priority ratings. Supplier is required to make every effort to deliver this material by this need date. FAR 52.211.15.
Q12 – DX DEFENSE RATED ORDER
This is a DX Defense Priority Rated order. The material is needed at the “ship to” location on the specified “delivery required” date. Supplier is required to give this order priority over unrated orders and orders with lower priority ratings. Supplier is required to make every effort to deliver this material by this need date. FAR 52.211.15.
Q13 – QUALITY MANAGEMENT SYSTEM (i.e., QMS)
Supplier is responsible for maintaining a documented QMS that complies with a nationally recognized standard (i.e., ISO9001 or AS9100), as applicable to the work scope stated in this order. The QMS shall also maintain a quality control system that inspects products prior to shipment to prevent delivery of non-conforming product. Notwithstanding the provisions of this clause, the Supplier is in no way relieved of the final responsibility to furnish the product, supplier, or services specified herein. Procedures, plans, and records will be made available for review by request of authorized Buyer representative. This system shall be subject to audit by Buyer’s Quality Assurance Representative.
Q14 – DRAWINGS/SPECS
A drawing/specification package must accompany parts when shipped to the Supplier. This same drawing/specification package must be returned by the Supplier with the parts. Note: These documents are controlled. Copying or otherwise altering these documents is prohibited unless prior authorization has been given by Buyer.
Q15 – DESIGNATED SOURCE
Buyer has delegated a Supplier QA Representative to be a Buyer Designated Source Inspector. This person has been issued a Buyer Delegated Source Inspector Stamp. The RDSI has been trained in Buyer’s Customer requirements and is responsible for compliance.
Q16 – NON-CONFORMING PRODUCT
Supplier must establish controls to assure that nonconforming materials are identified, segregated, dispositioned, and controlled to prevent inadvertent use or delivery. The Supplier shall immediately notify Buyer of any nonconforming product found in inventory from which product may have been delivered to Buyer. During performance, any deviations noted from established drawings or specifications must be reported immediately to Buyer. No deviations will be considered approved without written confirmation of the fact from Buyer. Under no circumstances are repairs to be taken without prior written approval. Rework that could adversely affect dimensional conformity must be communicated in writing and approved by the buyer prior to completion.
Q17 – 100% INSPECTION
Supplier is required to perform 100% Inspection on all parts supplied on this purchase order. Actual readings for all dimensions must be recorded and submitted with the associated parts on this order. In addition, inspection records must be retained for a minimum of seven (7) years, or as specified by the Buyer’s purchase order.
Q18 – FIRST ARTICLE
Supplier is required to submit a complete written 1st Article Inspection Report including 100% of the actual readings for all dimensions. The 1st Article Inspection shall be performed and documented per the requirements in AS9102. Report shall accompany the parts and reference Buyer’s purchase order number. Inspection records must be maintained by Supplier for a minimum of seven (7) years or as specified by Buyer’s purchase order.
Q19 – PROPRIETARY DESIGN
Supplier agrees not to make any change in materials or design details which would affect the part of any component part thereof with regard to (a) part number identification, (b) physical or functional interchangeability, and (c) repair and overhaul procedures and processes and material changes which affect these procedures without prior written approval of Buyer and without revising the part numbers and the originals of all drawings or data.
Q20 – TIME AND TEMPERATURE CHARTS
Supplier shall include quality evidence such as oven charts and data verifying conformance to the specified hardness, also known as Time and Temperature charts.
Q21 – SPC
Control Charts showing the current process capability (i.e., Cpk, Ppk) are required with each shipment. Each chart must reference Buyer’s part number, purchase order number, sample frequency and gage used. Where the process capability is below the industry standard (i.e., Cpk =>1.33, Ppk => 1.00) a certification of 100% inspection of that feature must be provided. Specific dimensions requiring SPC data collection will be listed or referenced on the purchase order. Sampling plans shall satisfy the requirements of ANSI/ASQ Z1.4 when statistical methods for product acceptance are used on parts, assemblies and components used on Buyer’s or its Customers products.
Q22 – MOLD IDENTIFICATION
Parts produced from multi-cavity molds must have mold produced markings that can be used for cavity identification and traceability.
Q23 – SHELF-LIFE ITEMS
These may include adhesives, paints, varnishes, enamels, conformal coating and etc. If material is age sensitive either for shelf-life storage or after the container is opened, material must be identified on container or separate batch/lot certification. Also identify date of manufacture either on container or separated certification packaged with each lot or shipped. If the product is not age sensitive, state this on the certificate.
Q24 – CERTIFICATION OF TEST EQUIPMENT AND MEASUREMENT STANDARDS CERTIFICATE OF CALIBRATION
The Supplier shall submit a certificate of calibration when product acceptance is solely based on the Supplier’s inspection data. At a minimum the certificate shall include Buyer’s purchase order number, equipment ID, equipment name/type, calibration due date, a statement that master gages are traceable to NIST standards and a statement of compliance to a certified QMS standard.
Q25 – INTENTIONALLY LEFT BLANK
Q26 – FLOW DOWN REQUIREMENTS
All Purchasing and Quality clauses indicated on the purchase order as well as requirements and specifications cited on prints and/or drawings must be flowed down to sub-tier suppliers.
Q27 – CORRECTIVE ACTION (CA)
Acceptance of this Purchase Order obligates the Supplier to perform, upon request, a corrective action investigation when discrepant product is received by Buyer. A written report shall be furnished with a reasonable time period to complete the corrective action to prevent reoccurrence. Supplier may use their own internal CA form provided it has at a minimum the following items;
• Buyer Purchase Order number
• Buyer CA number
• Supplier CA number
• Description of the nonconformance
• Root cause investigation notes
• Action(s) being implemented
• Date of completion for each action.
Q28 – DOCUMENT CONTROL
Supplier shall receive written approval from Buyer when it is determined that their internal documentation will be used as objective evidence provided to the customer to document design, process, and/or quality data for the product identified on the purchase order.
Q29 – RECORD RETENTION AND DISPOSITION
Supplier shall maintain all records of design, production, and inspection for a period of no less than seven (7) years. Buyer, its customer, and regulatory/statutory agencies reserve the right to the Supplier’s facility and all quality records pertaining to this purchase order. Record disposition must be performed in accordance with export regulations, i.e. ITAR.
Q30 – SURVEILLANCE/RIGHT OF ENTRY AGREEMENT
The authorized Quality Representative or relevant authority of Buyer shall have the right to maintain cognizance over the Quality Assurance inspection system imposed on the Supplier. Accordingly, the Supplier is expected to grant the designated representative access to their facility at all reasonable times and access to areas where the production of the item(s) covered by the Purchase Order is taking place. Where these areas infringe on the Supplier proprietary processes of a sensitive nature, or involve security with respect to other Supplier products being fabricated, mutually satisfactory arrangements shall be made with Buyer. The Government and/or Buyers’ Customer have the right to inspect any or all of the work included in the Purchase Order at the Supplier’s facility.
Q31 – INSPECTION RESULTS REPORT
The supplier shall furnish a stamped /signed and dated report of inspection results for each lot of parts shipped. Actual results are preferred where practical. Format is optional and can simply be a copy of the Supplier’s inspection records.
Q32 – DOCUMENT LEDGIBILITY
Supplier shall provide documentation that is legible and readily identifiable (e.g., Certificates and Reports).
Q33 –RAW MATERIAL CHEMICAL/MECHANICAL PROPERTIES LIMITS
Supplier shall ensure that Chemical and Mechanical properties for the raw material are guard banded no less than 3% of the minimum and/or maximum properties defined on the raw material certificate from the manufacturer.
Q34 –ROHS/REACH Compliant
Supplier shall be ROHS/REACH compliant. The supplier certificate of conformance shall state ROHS/REACH compliant, or a separate statement on company letterhead may be acceptable at the Buyers discretion.
Revisions
Rev. | Author | Date | Summary of change
A MLZ 6/5/2017 Initial release
B MLZ 7/26/2017 Moved Q25 to PURC4002 T&C
C JSR 11/13/2020 Update Q29 to include Disposition
D JSR 8/30/2021 Update Q01 to include revision
E JSR 6/7/2022 Add P17 and Q34 ROHS/REACH
F JSR 10/25/2023 Updated Email address in Q05, removed ISO9001 revision reference in Q13, Added rework to Q1
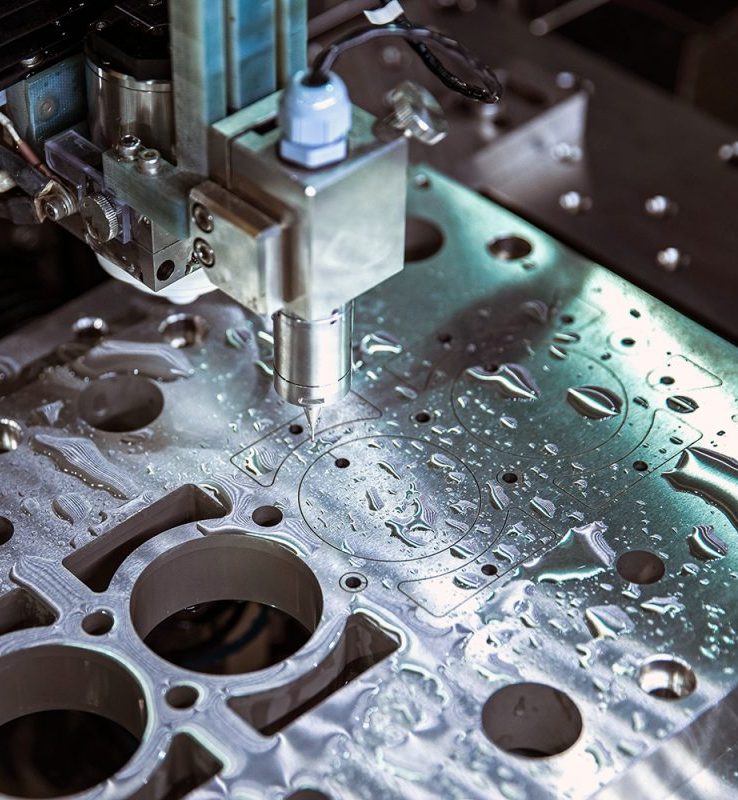